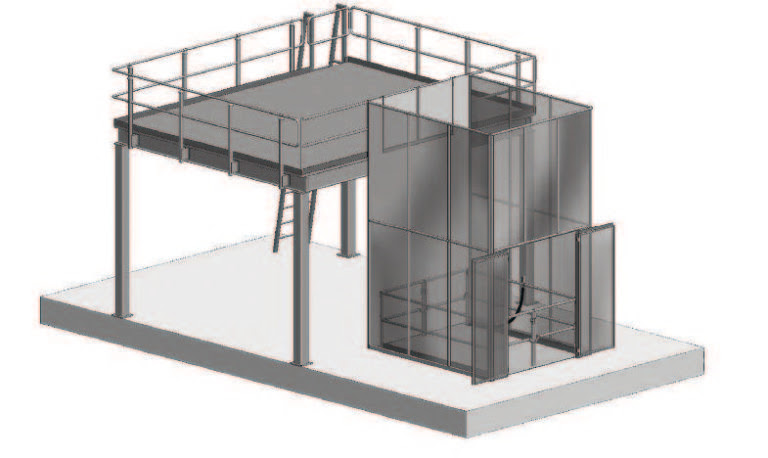
Rider mezzanine access lifts
How to get personnel and material from ground level to mezzanine level quickly, safely, and efficiently
Scissors lifts have been moving men and material from ground level to higher elevations for more than 60 years. They offer a distinct advantage over vertical reciprocating conveyors because people ride industrial scissors lifts along with the materials that they are moving. This greatly enhances the utility of the mezzanines. The cost is very competitive with VRC’s and the installation can offer significant savings because industrial scissors lifts come from the factory fully assembled instead of in kit forms like elevators and some vertical reciprocating conveyors so they avoid costly field assembly by elevator installers. Only the gates and enclosures need to be assembled on-site.
Three main features make industrial scissors lifts different from other kinds of lifts:
- Scissor lifts are fully assembled at the factory and not field assembled from kits.
- Scissors lifts have no external guide rails and/or pulley mechanisms to entangle riders. All the stability and lifting is provided by the scissors lift mechanism beneath the platform.
- Rider scissors lifts use constant pressure push buttons which means the rider operator is in constant control of the lift movement.
Governing codes
The International Building Code for 2015 was printed in June of 2014 and has clarified matters greatly. Chapter 30 Elevators and Conveying Systems, Section 3001.2 Referenced standards, sites ANSI MH29.1 Safety Requirements for Industrial Scissors Lifts. This clears up any confusion with other codes such as ASME17.1 for elevators, ASME B20.1 for vertical reciprocating conveyors or ASME 90.1 for other types of scissors lifts. Virtually all states, counties and municipal agencies accept the references cited by the International Building Code because they respect the rigorous (multi-year and multi-constituency) review process conducted by the ICC (International Code Council).
Note that the MH29.1:2012 was the standard reviewed and accepted and that this version differs substantially from previous versions.
Also, note that other codes such as those governing the height of guardrails or enclosures on mezzanines or upper floors must be reviewed in conjunction with the industrial scissors lift code. Enclosure heights at upper levels may vary in different jurisdictions.
The essential ingredients of a proper mezzanine lift
One of the essential ingredients of a proper mezzanine lift is a properly configured industrial scissor lift. The platform should be equipped with 42” high guardrails with mid rails and 4” toe plates. The lift platform should have electrically interlocked gates that prevent lift movement unless the lift gates are closed. The interlocked gates are not required by code but will be a common sense addition required by most municipalities and inspectors. The unit should have proximity switches or limit switches for each level. The control shall be a constant pressure pushbutton that the rider operator must keep depressed to maintain movement of the lift (the use of call/send buttons is not allowed with riders on the lift). The lift should also be equipped with an emergency down valve on the power unit to lower the lift in case of power failure. Again, this is not a code requirement, but most municipalities or inspectors will require it.
Another essential ingredient of a proper mezzanine lift is a smooth mezzanine fascia. The entire surface of the mezzanine adjacent to the lift from ground level to the top of the guardrail on the upper level must be equipped with a smooth face to eliminate shear points. This may be wallboard, polycarbonate GP sheets or fine mesh. Interlocked doors & windows are allowed.
A proper mezzanine lift would also include an enclosure system. The sides not adjacent to the mezzanine must be enclosed from ground level to the height of the highest guardrail in the fully raised position. The guardrail on the mezzanine and the access gates on the enclosure must be electrically interlocked to prevent lift movement when the gates or doors are opened and mechanically locked so that they cannot be opened unless the lift platform is present. The gap between the platform and the mezzanine should be 1”. The gap between the platform and the enclosure on all other sides should be approximately 3” to 4”. This gap requirement is not by code, but another common sense requirement required by most inspectors.
The configuration should look like this:
Advance lifts will always supply a configuration drawing after receipt of order so that users and inspecting authorities can make comments before the equipment is built and shipped.
What about inspections of these lifts?
Advance Lifts has studied elevator inspection forms from several states and realized that the forms closely followed the underlying elevator code. Advance Lifts then developed an inspection form following the same reasoning based on the latest draft of ANSI MH29.1. This form was then reviewed by elevator inspectors and further refined into its current form which is called the “Inspection Checklist For Industrial Scissors Lifts At Mezzanines” form AL-2010 Rev 1. This should be a big help to elevator inspectors and municipal building commissioners around the country.
Landing lock option
All multistage scissor lifts have some sway and some deflection inherent to their design. The BFL models typically used in mezzanine access lifts are exceptionally stout and rigid, but there still is some sway and deflection. This is by no means dangerous, but some people find this undesirable. Therefore, Advance Lifts created a Landing Lock (patent pending) which consists of two (2) locking pins that are extended into receivers when a unit arrives at an upper elevation. This eliminates sway and deflection at the loading edge of the platform. A discussion about specific applications is necessary to determine a recommendation on this option.