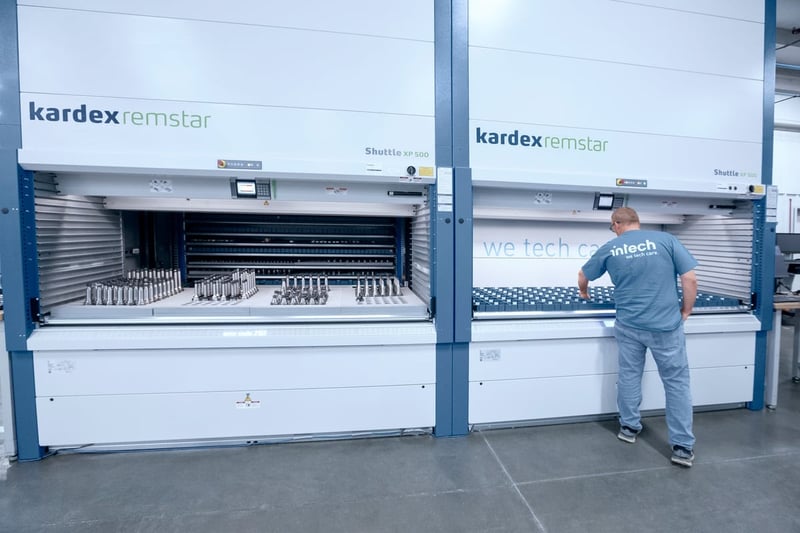
Precision, productivity, and progress: Intech’s inventory transformation journey with Kardex Remstar and ZOLLER
By integrating Kardex Shuttles with ZOLLER TMS Tool Management Solutions Software, Intech Athens has taken a monumental leap in streamlining inventory management processes, positioning them at the forefront of efficiency and precision in their industry.
Through their dedication to delivering exceptional services and driving innovation, Intech has grown into a global leader in orthopedic contract manufacturing. One of nine global facilities, the Intech contract manufacturing facility in Athens, Alabama (formerly known as Turner Medical) specializes in the meticulous manufacturing of complex medical device instrumentation. As a distinguished medical device job shop, Intech Athens contracts for the production and manufacturing of medical device instruments essential for orthopedics, from complex hip and knee robotics devices to expandable spinal implants.
Working at the intersection of medical science and engineering, Intech Athens plays a critical role in medical device innovation and production. Physicians, entrusted with the care of their patients, collaborate with industry-leading medical device Original Equipment Manufacturers (OEMs) such as Stryker and Medtronic. These medical professionals provide invaluable feedback—whether it’s developing a new surgical technique or a desire for a screw to fasten more swiftly, a tool to be more lightweight, or a design alteration to enhance accessibility during surgical procedures.
The OEMs, armed with this feedback, turn to Intech Athens to make it happen. The team at Intech Athens uses their expertise and creativity to meticulously prototype the envisioned instrument for physicians to test on cadavers, ensuring utmost precision and safety. It’s amazing to watch an idea transform: from a prototype birthed within prototype dedicated cells (branded The Prototype Garage®) at Intech Athens, through the initial production stages, to its eventual market launch. The pinnacle of this journey is the patient whose quality of life has improved thanks to an implant or instrument crafted in this very facility—it’s an unparalleled reward. This is where the real essence of Intech’s work shines through, where every effort becomes profoundly meaningful.
The Challenges of Rapid Growth
To support this endeavor, Intech Athens boasts a 100,000-square-foot facility including a robust production area with over 70 CNC machines as well as engineering, quality assurance, regulatory compliance, and customer service – all supported by just over 220 employees (proudly known as Intechers). Intech’s commitment to innovation and investment in new technologies is paying off – Intech Athens has experienced an extraordinary 150% growth in the past decade.
Amidst the rapid growth at Intech Athens, a new challenge became increasingly evident: the intricacies of inventory management. As the business expanded and the facility dove further into sophisticated manufacturing, inventory complexities multiplied.
Transitioning from manual machining to CNC (Computer Numerical Control) machine manufacturing impacted the volume and variety of tools and supplies required. Each piece of CNC machinery had its own ecosystem: the cutting tool, its collar, the holder it sits in, the nut fastening it together and the retention knobs on the holder anchoring it into the machine. Beyond this, there is the work holding – including quick-change fixturing, vices, clamps, and an array of other components. Additionally, to ensure each product meets rigorous standards, very specific and elaborate gauging systems are essential. What appeared as a single manufactured component was, in reality, a culmination of 100+ manufacturing tools, gages, and supplies.
Initially, Intech Athens used the traditional approach to manage inventory. Cabinets were grid-organized for less valuable smaller items while standard industrial shelving held larger items like fixtures and vices. Items were cataloged on clipboards and checked out manually, and it was expected that staff would conscientiously return them post-use. But as is often the challenge with manual systems, reliance on individual discipline and manual organization proved to be unreliable. Tools weren’t always returned to their designated spots, making it increasingly hard to locate specific items or determine their condition. Regular maintenance became an uphill battle.
Recognizing the need for enhanced control, Intech Athens installed a vending machine system for cutting tools. These smart vending cabinets would vend specific tools based on several inputs, streamlining the process to a degree. However, this only addressed a fraction of the inventory.
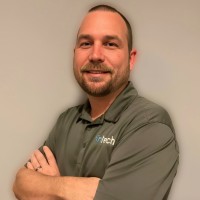
Joseph Forsyth
It wasn’t just about having the necessary tools—it was about knowing their exact location, quality, and readiness for use. “We were like any other job shop, we had the necessary items, but often didn’t know their location or condition. We knew we needed to do better,” said Joseph Forsyth, the Director of Advanced Manufacturing at Intech. Despite their growth and successes, Intech Athens found itself grappling with inventory control, a challenge they were determined to overcome.
Revolutionizing Inventory Management
To get control of their inventory, Intech had planned to leverage the ZOLLER Tool Management System software solution just as the Intech Toulon facility in France had done. But Intech Athens went a step further by integrating the ZOLLER TMS solution with high-density automated storage solution from Kardex Remstar.
Stepping into the future of inventory management, they replaced their traditional racking systems and most of the cabinets with two state-of-the-art Vertical Lift Module Kardex Shuttles. Working in harmony with the ZOLLER TMS software, this complete solution not only provided better inventory control but also delivered significant space savings and increased manufacturing productivity.
“From cutting tools to collars, vise jaws to sandpaper, and even dead blow hammers, we store them in the Kardex Shuttles. Through the ZOLLER TMS software, we’ve cataloged over 10,000 different part numbers. We now have unwavering clarity on our inventory—knowing precisely what we have and, more crucially, its exact location,” said Forsyth.
Inventory Control Increases Speed to Market
When it comes to medical device manufacturing, ‘speed to market’ is more than a catchphrase—it’s a determining factor of success. Particularly in prototyping, where swift turnarounds can be the difference between seizing an opportunity and missing out. For Intech Athens the reliability of their inventory control system is critical.
“It’s not just about having the necessary items on hand. The real challenge is the speed at which we can access accurate data about the inventory. It’s about answering questions like, ‘Do we have the required tool for this specific prototype?’ or ‘How many of this particular item are on hand?’ and crucially, ‘Where exactly is it located?’” says Forsyth.
The integration of the Kardex Shuttles with the ZOLLER TMS software has infused trust and accuracy into the inventory system in Intech Athens. Whereas previously, information might have been scattered across spreadsheets, on clipboards, or purely on the ‘honor system’, now the majority of the physical items in the shop, encompassing roughly $1.4 million worth of inventory, are systematically physically stored within the two Vertical Lift Module Kardex Shuttles and cataloged in the ZOLLER TMS software.
Now, with a simple click, any item can be located, its quantity ascertained, and its availability confirmed. This efficiency isn’t just about saving time—it’s about ensuring that the production process is unhampered —optimizing the speed to market.
Making Room for Innovation
As Intech Athens expanded its operations, the challenge of accommodating a growing inventory became a pressing concern. “The rate at which inventory was growing meant that space had become a premium. We were in a situation where new CNC machines were on hold because we literally had no room for them,” reflected Forsyth.
The introduction of two Kardex Shuttles proved to be a game-changer. Forsyth and his team embarked on a mission to declutter and organize, utilizing the ZOLLER TMS to inventory items and then transferring the items physically to the Kardex Shuttles. This strategic move instantly reclaimed an astonishing 10,000 square feet. Now, 80% of Intech’s inventory is managed in only 5% of their overall space.
Forsyth recalled, “The visual transformation was incredible. Racks and cabinets that once cluttered our space, enough to fill an entire 18-wheeler truck, now stood outside in the gravel parking lot. With this newly freed space, we were able to accommodate two more CNC machines, enhancing our production capabilities even before our planned facility expansion was finalized.”
Boosting Productivity with Renewed Focus
With the integration of the new inventory management system, production jobs are pre-staged days in advance increasing overall manufacturing productivity. “Previously, the 3-person pre-stage team was barely able to pre-stage production jobs for 60 machinists, now they handle pre-staging for 70 machinists easily,” said Forsyth.
Now, when the CNC machinist is ready to start production, the items they need are there waiting in the work cell. No longer do they have to disrupt their manufacturing process to search for the necessary items. “Machining these parts is complicated and challenging – it takes constant focus,” says Forsyth, “any distraction not only compromises focus but also translates to lost time and increased costs.”
In addition to streamlining CNC manufacturing, the new inventory system has unexpectedly turned into a valuable discovery tool. Particularly in the finishing and prototyping areas where a machinist’s role verges on artistry and the toolset at their disposal can influence their approach and outcomes. Before the integration of the Kardex Shuttles, tools, and supplies were often stowed away in cabinets, remaining unseen and underutilized. Forsyth recalls instances where staff would painstakingly work on a project using outdated methods, unaware that a tool within their inventory could accomplish the task in a fraction of the time.
Now, the organized trays not only store but can also showcase the tools and supplies available. Employees can physically access trays and ‘window shop’, encouraging them to explore, discover, and continuously educate themselves. Forsyth emphasized, “Our employees can freely navigate the trays, constantly updating themselves. It’s not uncommon for someone retrieving a tool to get captivated by another, thinking, ‘Wow, I didn’t even know we had these!’ It’s contributed to keeping that curiosity and knowledge alive within our employees.”
From Manual Search to Automated Precision
When a product is contracted and enters the production phase, the first task lands with the pre-stage group. This group strategically arranges the production jobs according to priority. They are aided by the ZOLLER TMS software, which provides a digital roadmap for each part detailing all the necessary tools and items required for its production.
Previously, a pre-stage operator would manually walk through the shop, opening various cabinets and sifting through boxes to locate the tools required for a specific production run. This process was tedious and prone to errors.
With the new Kardex Shuttles integrated with ZOLLER TMS software, this process has been transformed. Now, the pre-stage operator enters the job number into the ZOLLER TMS software, which is seamlessly integrated with the Kardex Shuttles. The system then directs the Kardex Shuttles to retrieve every item necessary for the part’s production.
As a tray is presented to the operator, integrated pick-to-light technology guides the operator to the specific item to be picked – identifying the part location and quantity to be picked. The operator selects the item, confirms its retrieval, and places it on a cart. This process is repeated until all items required for the job are picked, ranging from as few as two tools to as many as 70, depending on the complexity of the part. The cart with all of the required items is delivered to the work cell so the machinist can begin the job when ready.
Within the ZOLLER TMS software items can be retrieved in two ways – they can be checked out or issued out. When an item is checked out it’s a worn item meaning it is out of the system forever. When an item is issued out, the item is assigned to a job number and work cell. Issued items will be returned to the inventory management system after the job so they can be used for another job in the future. This feature allows Intech Athens to track the lifetime usage and location of issued items, such as cutting tools.
Centralized Prestaging with Decentralized Tooling
Unlike the traditional tool room concept where tools are clustered in a single centralized area of the facility, Intech Athens has created a unique combined approach. While the pre-stage team works from a centralized bulk supply in the Kardex Shuttles for initial tooling, replenishment tooling is additionally placed in smart cabinets across the shop floor. This strategy ensures that machinists have quick access to tools near their workstations, reducing wait time and improving efficiency.
The Kardex Shuttles serve as the primary centralized bulk storage solution, holding a month’s worth of tools and supplies. For instance, if Intech Athens purchases 100 of a particular tool monthly, 80 would be stored in the Kardex and 20 placed at decentralized points of use on the shop floor. In the event of a short pick at one of the shop floor locations, machinists can access the primary bulk supply in the Kardex Shuttles.
Expansion for the Future
What was once a cumbersome and often unreliable process is now seamless and efficient. The Kardex Shuttles in combination with the ZOLLER TMS software translates to improved inventory control, significant space savings, and increased manufacturing productivity.
Looking toward the future, Intech Athens is expecting delivery of a third Kardex Shuttle to be used in sub-assembly.. “We plan to start storing our completed jobs in a 25-foot Kardex Shuttle using the ZOLLER TMS software, as a place to hold them while they wait for the other parts required to complete sub-assembly,” says Forsyth. “It’s going to save us more square footage than anything we’ve ever done.”
In an industry where every second counts, Intech’s investment in integrating Kardex Shuttles with ZOLLER TMS software is more than a technical upgrade. It’s a declaration of their commitment to precision, efficiency, and above all, delivering speed to market.
About the Author
Kardex is a leading intralogistics solution provider of automated storage, retrieval, and material handling systems. With two entrepreneurially managed divisions, Kardex Remstar and Kardex Mlog, the Kardex mission is to provide solutions and services to increase the efficiency in storing and handling of goods and materials on a global scale.
The two divisions serve as partners over the entire life cycle of a customer’s product or solution. From project analysis to realization and service, Kardex helps improve a customer’s performance every step of the way. With three production plants in Germany and one in North America Kardex ensures high-quality solutions. To maintain and strengthen its competitive position within technological innovation and outstanding customer loyalty, Kardex is investing in research and development, its supply chain, the expansion of its service organization as well as in new technology via acquisitions. Kardex actively partners with global leaders who share the same values and complement the Kardex solutions including AutoStore, Rocket Solution, Intertex and Sumobox.
Kardex employs 2,000 team members across 30 countries and has installed over 140,000 industry-specific solutions worldwide.