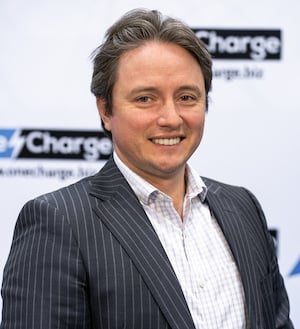
Leaner manufacturing with lithium batteries
16600 Aston
Irvine, CA 92606
http://onecharge.biz/
The recent advances in lithium industrial batteries and their use in manufacturing are remarkable. So much so, that it may become the single most important hardware step-change of the past few decades.
By switching a forklift fleet to lithium power, a company can considerably improve its overall financial results, productivity, while lowering maintenance, operational costs and also create a safer workplace environment – all at the same time.
Manufacturing is a major part of the US economy, accounting for 11%* of GDP. Over the last three decades, the industry has undergone a lot of transformations, as companies apply new technologies and methodologies to improve operations.
The need for higher efficiency
Balancing rising raw material costs and other margin stressors
As manufacturing becomes more cost-sensitive and customers demand quality, increasing-price pressures result in lower margins.
If we add a recent increase in steel and raw material costs to this equation, the picture becomes even more complicated for the bottom line, so it is important to find effective ways to reduce costs and improve efficiency at plants.
Managing the material handling fleet inventory is still an opportunity to improve the efficiency of operations in the manufacturing industry. Many companies are adopting autonomous guided vehicles (AGVs) and autonomous mobile robots (AMRs) powered by lithium batteries.
Flexible fast charging patterns offered by Li-ion batteries can always be tailored to meet your schedule of operations, not the other way round. Together with zero daily maintenance, a switch to lithium batteries can increase uptime and improve efficiency, allowing you to focus on operations and forget about the battery.
The use of AGVs and AMRs also addresses the long-standing issue of a labor shortage—and Li-ion is the best choice of motive power to pair with various automated applications. By deploying ergonomic Li-ion solutions, not only you can reduce operating costs, but also redirect your workers to more value-added tasks.
Extending the lifespan of equipment
Today, lithium-ion industrial batteries are the most cost-efficient choice for many operations with multiple forklifts working multiple shifts. Compared to the older lead-acid technology, they offer better performance, increased uptime, longer lifespan, and lower total cost of ownership.
One Li-ion power pack can replace several lead-acid batteries and it also has a 2–3 times longer life span. Your equipment will also serve longer and require less maintenance with lithium batteries: they guarantee less wear and tear on the forklifts with stable voltage at any level of discharge.
Increasing equipment utilization with “just right” forklift fleet configuration
Li-ion technology enables the flexible configuration of a power pack for any specific task and type of material handling equipment used in manufacturing. “Just in time” manufacturing can now be supported by a “just right” fleet of forklifts. In some cases, companies can achieve considerable savings by reducing the fleet to do the same job. This is exactly what happened when Standard Distributing Co switched to Li-ion batteries and reduced the number of forklifts by 30%.
With lithium batteries, you only pay for what you need. When you know the exact daily energy throughput and charging patterns of your forklifts, you set on minimum sufficient specs, or opt for higher capacity to have a cushion for contingency and ensure a longer lifespan for the battery.
Due diligence in a power study of your material handling operations can help to choose just the right battery specs for your fleet and application. Modern lithium batteries are Wi-Fi enabled and can provide fleet managers with reliable data on the state of charge, temperature, energy throughput, the timing of charging and discharging events, idle periods, etc. OneCharge lithium batteries offer a fully customized solution to many applications to ensure maximum equipment utilization.
Safety and Sustainability
The manufacturing industry is following the eco trends with the rest of the world. Many corporations are introducing measurable sustainability goals, including the reduction of their carbon footprint, the use of cleaner and safer processes and equipment, and transparent waste management and disposal.
Li-ion batteries are a non-toxic, safe, and clean power source, without the risks of acid fumes or spills associated with overheated lead-acid batteries or human error in their daily maintenance. Single battery operation and the extended lifespan of a lithium battery mean less waste. Overall, 30% less electricity will be used for the same job, and that translates into a smaller carbon footprint.
Case Studies
Aerospace manufacturer makes the switch to lithium batteries.
Spirit AeroSystems is one of the world’s leading designers and manufacturers of aerostructures, providing products and solutions for both commercial and defense customers, including Airbus and Boeing.
The company was constantly facing problems with maintenance and overall reduced runtime with the sealed lead-acid TPPL power units they had been using for the last 5 years. Facilities that use AGV lead-acid battery-powered fleets consistently face about 20% asset downtime.
The main reasons for switching to Li-ion forklift batteries were increased operational demands and operational issues brought about by lead-acid battery usage: too much time for battery maintenance, too much downtime, too much hassle, and too much space dedicated to storage facilities.
With the new Li-ion technology, they managed to sync the production schedule with battery charging. It only takes 1–1.5 hours to fully charge a battery once or twice per day. Li-ion batteries can stand much more abuse and need much less attention than lead-acid batteries. ROI calculations and the overall stability of OneCharge Li-ion batteries were the main reasons Spirit AeroSystems chose OneCharge.
Li-ion batteries improve warehouse efficiency by 5% for a leading U.S. manufacturer.
Briggs & Stratton, a U.S. small engine manufacturer, merged its smaller warehouses across the U.S. into two large distribution centers. The decision to switch the entire fleet from lead-acid batteries to Li-ion forklift batteries was based on a detailed cost analysis. OneCharge lithium batteries demonstrated significant savings, reducing the total cost of ownership compared to both LPG (propane) and lead-acid batteries. After a year and a half of impeccable performance from OneCharge Li-ion Batteries, the company has seen a 5% overall efficiency increase in warehouse operations, according to Bill Harlow, Director of Distribution & Warehousing at Briggs & Stratton.
Benefits for a manufacturing company switching to Li-ion batteries in its material handling operations:
- Minimum downtime reduced operational costs
- Improved operational planning thanks to flexible charging
- “Just right” equipment configuration based on cutting-edge data capabilities
- Automation-readiness—a perfect fit for AGVs and AMRs
- Safe, clean technology that satisfies the top hygiene standards