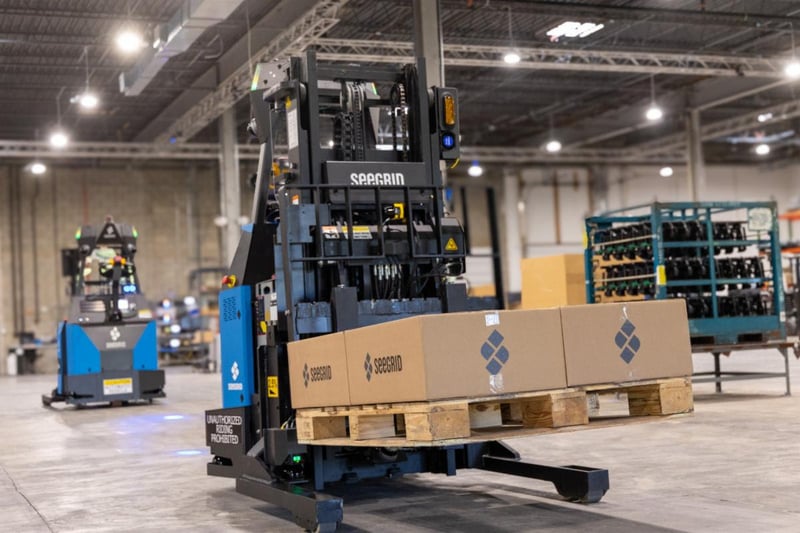
How Autonomous Mobile Robots are overcoming labor hurdles in manufacturing and logistics
Addressing labor challenges and enhancing operational efficiency are crucial priorities in manufacturing, warehousing, and logistics. Automating the palletized material workflow plays a significant role in achieving these objectives. Advances in robotic lift truck technology are empowering modern industrial facilities to reach unprecedented levels of efficiency, productivity, and safety.
Facility operations have long desired to bring autonomy to palletized material flows within their environments. Over time, the technology available to achieve their automation efforts has progressed to a broad set of options, ranging from the highly predictable but infrastructure-laden Autonomous Guided Vehicles (AGVs) introduced a half-century ago, to the highly flexible and infrastructure-free LiDAR/SLAM Autonomous Mobile Robots (AMRs) available today.
Let’s take a closer look at autonomous lift truck AMRs and how they can combat the labor crisis. These advanced lift trucks introduce greater capability, safety, and scalability, enabling facilities to tackle labor challenges, achieve operational goals, and bolster a competitive edge. They also enhance productivity and reliability in the workplace by ensuring efficient, consistent material movement and minimizing downtime.
Rising Labor Challenges
Autonomous lift trucks are proving effective in addressing the three biggest labor challenges impacting manufacturing, warehousing, and logistics operations: labor costs, labor availability, and safety.
Labor Costs: As labor costs continue to rise, particularly in unionized environments, modern industrial facilities are focusing on strategic cost management and resource allocation. Lift truck AMRs present an opportunity to enhance operational efficiency while allowing companies to invest in their workforce more effectively. By automating highly repetitive tasks, facilities can redirect human talent towards higher-value roles and tasks that require advanced skills and independent thinking. This approach not only addresses cost concerns but also improves employee satisfaction by reducing monotonous work and creating opportunities for employees to engage in more stimulating and rewarding responsibilities across industrial manufacturing facilities.
Labor Availability: Attracting and retaining a reliable workforce is a major challenge, particularly in multi-shift operations with less desirable evening and night hours. Absenteeism leads to costly downtime. This is where autonomous lift trucks are another game-changer—they show up for every shift, on time, and deliver consistent performance without breaks or dips in efficiency or precision.
Safety: It’s all too common for humans to make costly, often dangerous mistakes when operating lift trucks. But lift truck AMRs simply don’t. Manual operators are responsible for over 25,000 accidents and nearly 100 fatalities each year. The shortage of skilled lift truck operators worsens the issue, as 25% of OSHA recordable incidents result from inadequate training. Consequently, manufacturing, warehousing, and logistics operations are increasingly adopting lift truck AMRs to automate their hazardous and inefficient workflows, thereby enhancing operational and workplace safety.
Strategic Benefits of Automated Lift Trucks
The strategic benefits of automated lift trucks extend beyond addressing labor challenges:
Direct Cost Savings: From straight labor savings alone, manufacturing, warehousing and logistics operations typically achieve an ROI payback from investment in lift truck AMRs within 24 months. In multi-shift manufacturing operations, the return can be achieved in as little as 18 months.
Added Financial Value: Lift truck AMRs bring powerful added value. Not only do they improve safety, but they also help prevent costly damage—avoiding collisions with each other, protecting payloads, safeguarding equipment, and steering clear of walls.
Strategic Impact: Transitioning to a more autonomous palletized material flow can significantly enhance the overall performance of facility operations. For instance, using lift truck AMRs improves the efficiency of parts-to-line processes, ensuring materials are delivered precisely when needed, potentially reducing inventory within the facility by 25 to 30%. These efficiencies result in vast inventory cost savings and more optimal use of space.
The strategic benefits of automated lift trucks extend beyond labor challenges. They offer significant cost savings, enhance safety, and prevent costly damage. By improving material flow and process efficiency, lift truck AMRs can optimize facility operations, reduce inventory, and maximize space usage.
Challenges of Payload Manipulation
Reliably automating the pick-up and placement of forkable objects poses a significant technical challenge. This process demands advanced payload detection systems capable of properly recognizing and handling a wide variety of payloads. While standardizing on two-pocket wooden pallets would simplify the task, the reality is far more complex. In modern manufacturing environments there are thousands of “forkable objects,” pallets or other payloads intended to be manipulated by a lift truck, that do not resemble a stereotypical, perfect wooden pallet—posing a great challenge to autonomy. With countless variations of diverse forkable payloads, from open-air knock-down boxes to carts and various objects that bear no resemblance to a pallet, each task requires precise handling by autonomous lift trucks.
In addition to the limitless payload types, another challenge exists. The physical condition of the forkable object also varies considerably. Common wear and tear can quickly transform many pallets into shapes that don’t quite resemble pallets anymore.
Payload detection and manipulation are further complicated by the fact that forkable objects are often imperfectly placed by human operators. The pick-and-drop tasks frequently require precision and agility to adapt to the dynamic and variable positioning of goods. Effectively meeting these payload manipulation challenges requires intelligent AMRs designed for flexibility and adaptability, equipped with advanced LiDAR/SLAM sensors and sophisticated tech stacks.
Efficiency for the Long Haul
Efficient payload handling is crucial for acquiring and accurately positioning a payload. However, distinct capabilities are needed for transporting between pickup and drop-off locations, often over long distances. While flexibility is essential for pick and drop tasks, long haul movements of payloads demand a different capability of excellence—predictability.
Predictability is an area where Automated Guided Vehicles (AGVs) have traditionally been known to excel. These vehicles follow fixed paths defined by requiring physical infrastructure like magnetic strips, wires, or reflectors to name a few, implemented into a facility. AGVs provide ideal solutions for repetitive tasks in structured environments, where their unwavering adherence to predetermined routes minimizes deviations and ensures a consistent, predictable workflow.
The most effective autonomous industrial vehicles can navigate with the predictability of an AGV, but remarkably without any magnets or other physical infrastructure. Seegrid pioneered this innovation in 2008, with the introduction of the Grid Engine. This 3D probabilistic mapping technology facilitates precise indoor localization for vehicles in industrial settings.
The Best of Both Worlds
The ideal solution doesn’t force modern facilities to choose between the predictability of traditional AGV’s or the flexibility of modern AMRs. Unique-to-Seegrid Sliding Scale Autonomy technology merges these two paradigms to offer an innovative hybrid approach that adapts to the specific needs of the application at hand.
Additionally, Seegrid’s industry-leading pallet and payload detection system allows lift trucks to pick and move the widest array of forkable objects in the market today without the need for any additional infrastructure.
The Future of Autonomous Palletized Material Handling
It’s no longer a matter of “if” autonomous workflows should be adopted—it’s a matter of how and when. The more autonomous a facility becomes, the more benefits and ROI can be expected—from overall operational cost and inventory reduction to reliable throughput and predictability. Autonomous lift trucks, in concert with other autonomous technologies, are facilitating full end-to-end workflow autonomy with the ability to adjust to increasing and changing demands of modern manufacturing, warehousing, and logistics facilities.
When considering the integration of autonomous systems into existing workflows, it’s important to understand the limitations and strengths of both human and machine capabilities. Autonomous vehicles and manual operators are not a 1:1 swap. As famously noted by Seegrid Founder Hans Moravec in what is known as Moravec’s Paradox, things that are easy for humans are very hard for machines, whereas things that are hard for humans are easy for machines. With this in mind, the best combination is for humans and machines to work alongside each other—with AMRs doing the mundane and often dangerous tasks, while humans are left to more cognitive roles.