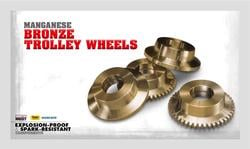
Explosion proof and spark resistance
There is some confusion regarding explosion proof and spark resistance. The following article explains the difference and gives some information on how to specify the classification of the application.
EXPLOSION PROOF
The “Explosion Proof” term defines the electrical enclosures, controls, motors and wiring requirements required to contain any spark or arcing from penetrating the confines of the enclosure and potentially igniting the combustible material present in the atmosphere.
SPARK RESISTANT
“Spark Resistant” refers to the mechanical and structural elements of the hoist or crane that could create a spark based upon usage. Friction between certain materials can cause sparks sufficient enough to ignite flammable gas or dust. A cigarette lighter or an antique flintlock musket are familiar examples of this. The type and concentration/dilution of gases in an area is one element that affects potential ignition from a mechanically generated source, but other key factors could include
-The type materials making contact
-The speed/pressure with which the materials come into contact
-Corrosion on one or more of the contacting surfaces
-Lubrication
Contact between steel surfaces can create sparks. Steel is commonly used in most hoists and cranes for load-bearing components such as hooks, lower blocks, load chain and trolley wheels, and therefore may not be suitable for some hazardous environments.
In the U.S., NFPA 70, part of the National Electric Code (NEC), addresses the design and installation of electrical conductors and equipment in hazardous areas but does not specifically provide guidelines for mechanical equipment used in these same hazardous locations.
APPLICATION
When an application requires a determination of an explosion proof Class, Group and Condition most hoist and crane suppliers and manufacturers require that the purchaser defines the hazard and the NEC classification. The requirement for spark resistance features also needs to be determined by the purchaser. Therefore, we recommend that purchasers thoroughly research the combustible sources in the operating environment and engage the professional opinion of a qualified engineer to determine the proper Explosion Proof Classification as well as Spark Resistance features.
Explosion proof and spark resistant features do not come cheap. Depending on the NEC classification, special motors, explosion proof enclosures, control pendants and safety limits may be required; sometimes doubling the price of the equipment. The capacity rating of the equipment can be reduced when stainless wire rope or chain is required for spark resistance since it is not as strong as the same parts in steel. Technology has helped in some classifications using intrinsically safe relays that preclude the need for very expensive, large and heavy explosion-proof components. Options to save money on spark resistant features include the use of copper plated hooks in lieu of very expensive solid bronze hooks.
Contact a CRANE 1 application expert who can walk you through the requirements and ensure that you receive equipment suited to your application.
NEC Explosion Proof Classifications for Equipment (Class, Group & Division)
- Class
- Class I – Locations: Are those in which flammable gases or vapors are or may be present in the air in quantities sufficient to produce explosive or ignitable mixtures.
- Class II – Locations: Are those in which are hazardous due to the presence of combustible dust.
- Class III – Locations: Are those which are hazardous due to the presence of easily ignitable fibers or flyings, but in which such fibers or flyings are not likely to be in suspension in the air in quantities to produce ignitable mixtures.
- Group
- Groups for Class I (above)
- Group A – Atmospheres containing acetylene.
- Group B – Atmospheres containing hydrogen, or gases (or vapors) of equivalent hazard, such as manufactured gas.
- Group C – Atmospheres containing ethyl-ether vapors, ethylene or cyclo propane.
- Group D – Atmospheres containing gasoline, hezane, naptha, benzine, butane, alcohol, acetone, benzol, lacquer solvent vapors, or natural gas.
- Groups for Class II (above)
- Group E – Atmospheres containing metal dust, including aluminum, magnesium and their commercial alloys and other metals of similarly hazardous characteristics.
- Group F – Atmospheres containing carbon black, coal, or coke dust.
- Group G – Atmospheres containing flour, starch, or grain dust.
- Groups for Class I (above)
- Division
- Division I – Locations in which hazardous concentrations in the air exist continuously, intermittently, or periodically under normal operating conditions.
- Division II – Locations in which hazardous concentrations are handled, processed, or used but are normally within closed containers or closed systems from which they can escape one in case of accidental rupture or breakdown.