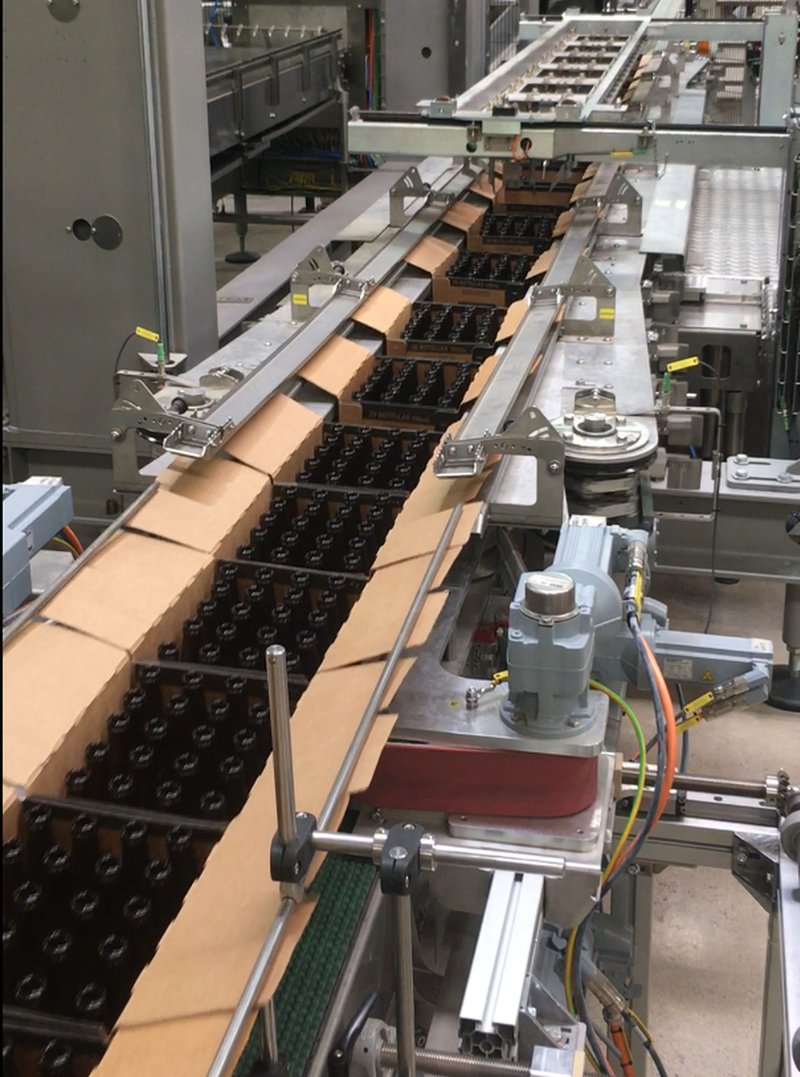
Avoiding bottle breakage: special trolley with spring assembly and customized drive chain positions cartons precisely on the pack conveyor
Permanent lubrication system reduces maintenance costs
A large beverage producer in Mexico invested in an automated system for packing and unpacking bottles from crates. They ordered their system from KHS, one of the world’s leading manufacturers of filling and packaging systems. In contrast to the more usual case, reusable cartons, which are much more stable, are used to transport the bottles instead of plastic crates. To enable the automated packers and unpackers to remove and insert the bottles gently and precisely, the Dortmund-based system supplier faced the challenge of finding a guide system that could travel very small radii (R=100) and right/left curves without play due to the limited installation space.
KHS therefore co-operated with PGM Motion and used their W-Line guideways. They integrated the rail systems with specially developed guide carriages as part of the prototype construction, which enable their systems to negotiate tight curves without any play. PGM Motion has developed special drive chains to drive the carriages.
“Most people in the world of beverage bottling in this country think of robust plastic crates that transport bottles safely from A to B,” says Joachim Öchsner, Managing Director at PGM Motion GmbH. But the reality is not the same everywhere: for example, reusable bottles were transported in cartons at a well-known drinks manufacturer in Mexico. These containers are less stable, which can cause difficulties during tightly synchronized transport automation. And that was also the case with the system that was to run on site at the bottler: “Cardboard boxes are much more unstable than plastic crates and so are already quite worn by the time they reach our production process. The difficulty now was to ‘divide’ these cartons in a way that was gentle on the product so that our packing system could insert or remove the bottles,” reports Stefan Habermann, Head of Design – Product Centre Palletizing Technology at KHS. “It is essential for the individual cartons to be positioned correctly on the pack conveyor so that the containers do not break and the conveyor belts rarely need readjustment.”
Carriages using traditional roller guideways have to be individually adjusted to the rails using eccentric bolts, and they are not able to travel on small radii with right and left curves without play or load resistance. The transitions at the joints of the guide rails also often have to be reground with an oil stone, which is very time-consuming. These systems were, therefore, not feasible in this application.
KHS turned to the drive specialists at PGM Motion to ensure nothing was left to chance.
Following intensive dialogue, PGM developed a solution specially designed for this application, based on a new design for the guide carriages and rail elements.
Special trolley enables play-free transport
“The crucial advantage of this solution lies in the introduction of a spring package that permanently presses the carriages onto the rail using pre-tension,” explains Öchsner. In contrast to conventional systems, where the play increases over time and the carriages start to wobble, the movement of the PGM solution remains stable in the long term. The guide carriage rollers are in permanent contact with the rail, both in straight sections and in changing curve radii. There is no need to set eccentric bolts; the carriages are immediately ready for operation and can be replaced.
The cartons must be positioned precisely so that the packer and unpacker can lift and lower the bottles. The drive chain was therefore also adapted. A spring system enables the chain to elongate in the spring links, yet it remains robust enough not to be damaged by glass or shards.
A keyway is integrated at the ends of the guide rails to ensure precise transitions between the rail elements, eliminating the need for manual reworking. Individual rail segments can be replaced as required.
Permanent lubrication system replaces tedious manual maintenance
A permanent lubrication system is designed to prevent the carriages from wearing out over time. It ensures that grease is continuously delivered to the carriages. “The limited installation space made it impossible for the operator to reach all the necessary lubrication points. The PGM system takes over this task, making a reliable contribution to longevity and customer satisfaction,” explains Habermann.
Overall, PGM Motion’s solution not only successfully overcame the specific challenges of the project but demonstrated that other system series can also be easily customised. The high manufacturing precision of the guide rails and the integrated keyway enable quick and easy installation, as the rail elements fit together precisely. Since being commissioned in October 2022, the system has been running smoothly at the user in Mexico and no major challenges or failures have been reported. “We received excellent support at all times during this prototype development. We always felt that we were not just another customer, but that PGM Motion was just as invested in our success as we were,” summarises Habermann.