Yale Lift Truck Technologies has announced Yale Relay™, an overarching platform encompassing all automated lift trucks the company releases going forward and an intuitive drag-and-drop portal that replaces the complex software coding requirements typically associated with automation. The new portal enables easy setup and on-the-fly changes without custom programming, allowing warehouses to reduce their dependence on scarce warehouse labor without expensive software engineering resources. Attendees of the ProMat show in Chicago can get hands-on experience with the Yale Relay™ portal and automated tow tractors at booth #S647.
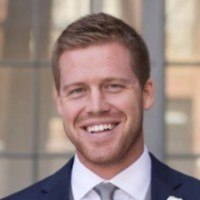
“This new solution represents a reboot of automated lift trucks, positioned to more efficiently meet demand for mobile automation by avoiding the labor and capital constraints of today’s market,” says Kyle Smart, Sales Manager, Emerging Technology, Yale Lift Truck Technologies. “Not only does Yale Relay address challenges sourcing lift truck operators and software programmers, it completely changes the financial commitment necessary for end users to deploy automation. Rather than a major capital expense, warehouses can simply pay by the month through a rental agreement and avoid the major upfront costs of purchasing equipment.”
Yale Relay results from almost a decade of customer-driven refinement, addressing the complexity, reliability and cost concerns traditionally associated with automated lift trucks. Whereas some solutions from robotic forklift or autonomous mobile robot suppliers may involve warehouses managing against disjointed integration, service from multiple stakeholders or long waits for offshore support, Yale Relay automated lift trucks are backed by training, parts, and maintenance through a single, local source – the Yale® dealer network.
The drag-and-drop portal allows for significantly faster startup than traditional approaches, enabling implementation in as little as a day. Mapping the facility is as simple as manually operating the lift truck along the desired route and dropping waypoints in the portal, and making changes is as simple as selecting a waypoint and dragging it to a new location. The portal provides cloud-based access that enables easy, efficient management of automated lift trucks across multiple facilities, and reduces the need for on-site interventions with remote monitoring and update capabilities. It is designed with the ability to integrate with other common warehouse systems like facility fire alarms, interactive input boxes, programmable logic controllers, warehouse management systems, and more.
The automated tow tractor is designed to handle horizontal load transportation tasks and includes several important features to reduce manual intervention, such as automated wireless charging and an available automated hitch and unhitch option. Sensors and other automation-related components are integrated separately above the body of the truck and designed for easy adjustment and maintenance.