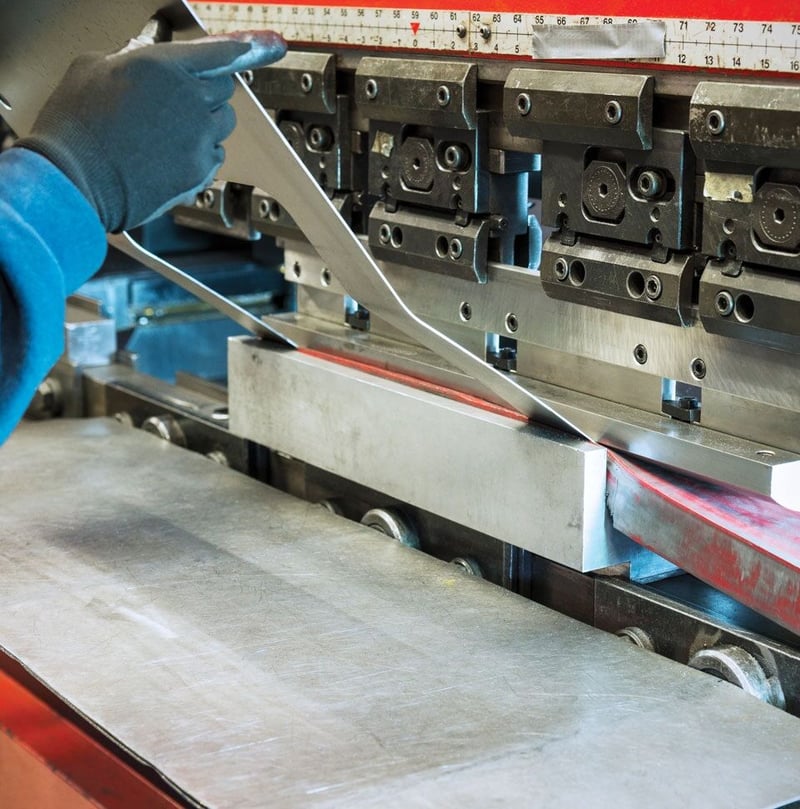
Rockford Systems launches Press Safety Inspection Service
Rockford Systems, a provider of machine safeguarding and combustion safety solutions, just announced the expansion of its workplace safety portfolio with a new Press Safety Inspection service.The Press Safety Inspection service will evaluate the current mechanical operation and safety compliance of punch presses and press brakes.
Presses are dangerous machines, much more so without proper safeguarding or maintenance. The U.S. Department of Labor reports that press operators suffer more than 350 amputations per year. The greatest threat linked to running presses and press brakes is having the operator’s hand trapped between the part being bent and the frame of the machine at the point of operation. If the force is great enough or the part is sharp enough, impalement or an amputation can occur.
Another key factor contributing to the dangers of presses is a lack of maintenance. An unmaintained press or press brake, especially one with damaged tooling, can put both the machine and operator at risk for serious injury.
Rockford Systems’ experienced inspectors will visit customers onsite to evaluate the mechanical operation and safety compliance of the organization’s presses. Based on a thorough analysis, the visual inspection will determine if part-revolution punch presses and press brakes, and full-revolution punch presses, are in safe working order according to OSHA regulations and ANSI standards. This determination follows a series of function tests including press stop times, safety distance measurements, and inspection of safeguards and controls. In addition, a visual mechanical inspection will assess the proper functioning of the press, condition of press lockout/tagout devices, safeguarding and controls, NFPA 79 electrical compliance, tooling or dies and their setups, and any auxiliary safeguarding.
According to Brian Boes, Vice President of Applications Engineering for Rockford Systems, “Every mechanical power press must be looked at as an individual system. Key areas of the visual inspection include frame and mechanical parts, electrical or electronic systems, hydraulics and pneumatics, mechanical linkages, counterbalances operating and used properly, dirt or water in air lines, proper operational speed, press production requirements, and maintenance requirements.”
This new Press Safety Inspection service helps organizations meet OSHA (29 CFR 1910.212 and 1910.217) regulations that require an employer establish and follow a program of periodic inspections of its press machines. This is done to ensure that the press, together with its auxiliary equipment and safeguards, are all in safe working condition and properly adjusted. An inspection by Rockford Systems also can ensure the equipment’s mechanical status and, as part of a preventive maintenance program, help prevent breakdowns that can lead to costly production delays.
The same OSHA regulation states that a press’ mechanical, electrical, pneumatic and hydraulic components and systems, including all collateral equipment, be kept in first-class operating condition. Furthermore, it is required that companies immediately replace or repair any part of a press that is worn, damaged or not operating correctly, before a press is used again.
Besides being an OSHA requirement, Boes noted that formal press inspections must be also made at regular intervals based on the press manufacturer’s recommendations.