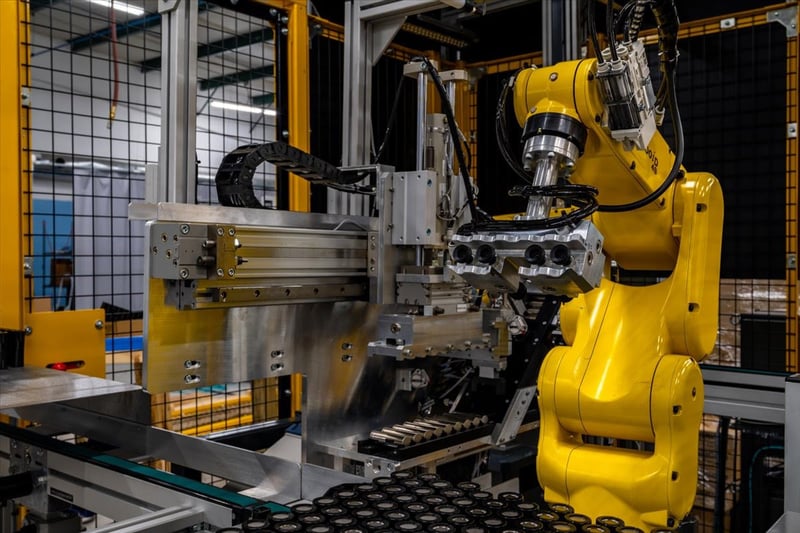
New battery test & assembly system from McAlister Design & Automation
The system enables pre-pack manufacturing testing of battery cells and battery cell performance data storage capabilities
McAlister Design & Automation, a subsidiary of Wauseon Machine, revealed its new Battery Test and Assembly System. This battery system enables the inspection and testing of battery cells and assembly of battery packs, commonly used in electric vehicles and consumer products. The system has been developed to support market changes and future growth.
The Battery Test & Assembly system allows battery pack manufacturers to ensure the quality of their product meets or exceeds the requirements for its design. The Battery Test and Assembly System tests each battery cell before incorporating it in the pack, mitigating the number of packs that falter because of a potential issue with a single battery cell.
McAlister Design & Automation designed this system in response to the rapid increase in demand for electric vehicles, power tools, and electronic residential equipment. The system utilizes industry-standard battery cell packaging, minimizing the amount of operator handling during the introduction to the testing and assembly process. Additionally, McAlister Design & Automation modeled the Battery Test & Assembly System around the 2170 battery for broader application benefits, including the many industries previously mentioned.
In today’s market, data tracking and storage enables traceability and is a critical aspect of manufacturing operations. This Battery Test & Assembly system features the capability to capture, store, and analyze battery cell and pack data. This grants manufacturers the ability to trace battery pack and cell performance over the entire life cycle of their product—enabling manufacturers to manage incoming supplier quality and trace defects across their value stream.
The system has a unique focus on flexibility—using vision guidance for robotic components, six-axis robots, and conveyors—allowing the system to be modified or reconfigured for varying battery sizes or battery pack configurations. The system design also features asynchronous testing and assembly stations, maximizing its throughput and minimizing the amount of time it takes to assemble a battery pack. Plus, its pre-engineered software makes for an easily scalable and adaptable system to accommodate hazardous lithium-ion batteries. The system offers integrated dunnage inspection, providing fire hazard mitigation and a safer working environment for system operators.