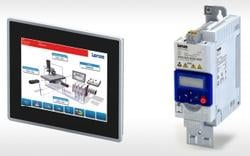
Lenze smart automation solution teams up panel controller and frequency inverter
A global manufacturer of electrical and mechanical drives, motion control and automation technologies, Lenze has introduced an intelligent automation solution package combining the Lenze p300 Panel Controller and the Lenze i500 Frequency Inverter. The smart solution integrates a PLC tooling interface to reduce engineering requirements and costly troubleshooting of automated machines and systems.
“In modern automation, smart development strategies must focus on creating easier, more compact and modular machine solutions. The combination of the p300 and i500 provides more automation with less effort—so customers can focus on what they do best,” said Daniel Repp, business development manager, automation solutions, Lenze Americas.
The intelligence behind the Lenze automation solution is the p300 Panel Controller, which unites the Codesys-based sequence control and visualization in a flat device. Designed for basic to medium complexity control and visualization tasks, the robust p300 provides for uniform engineering in all phases of the machine development process. Ready-to-use templates and libraries simplify the handling of visualization displays, with plain text diagnostic information presented in different languages. The space-saving p300 unit is designed for direct installation on the control cabinet door.
The Lenze i500 Frequency Inverter features a streamlined design and scalable functionality for suitable for such applications as conveyors, formers, winders, traveling drives, tool and hoist drives. This is Lenze’s newest inverter series in the 0.33 to 100 Hp (0.25 to 75 kW) power range.
The combination of the p300 and i500 simplifies engineering with a user-friendly tool for drive parameterization. Eliminating the need for knowledge of traditional programming languages, the Lenze PLC Designer makes online and offline parameterization straightforward. The PLC tooling interface on the p300 enables direct access to the i500, so parameters can be changed intuitively during runtime and saved in the control system for reference later. The PLC Designer allows device content to be written onto a USB flash drive and easily loaded into successive machines. EtherCAT standard interfaces between the p300 and i500 ensure faster control cycles and facilitate remote maintenance and monitoring.
“Project parameters can be stored on a back-up USB—saving valuable time for customers implementing series machine design and services,” adds Repp.