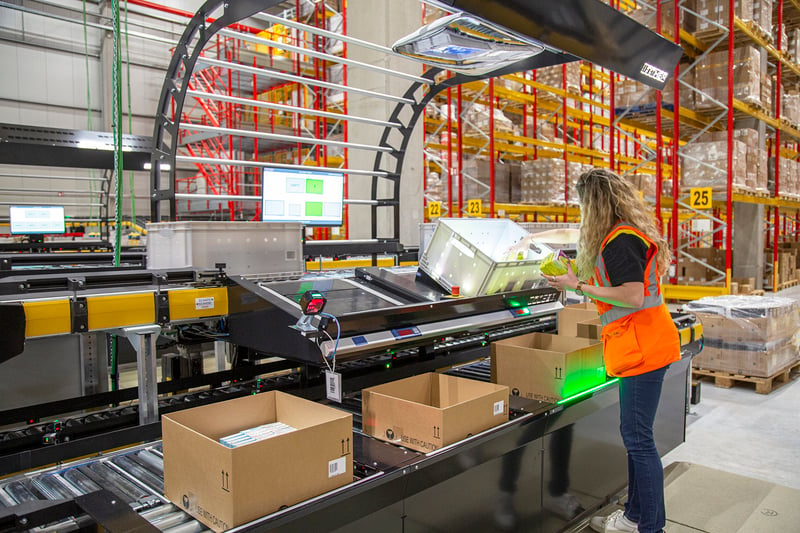
Inther Group provides futureproof DC for DHL Life Sciences
Two years ago, the starting signal was given for the completely new warehouse for DHL Pharma Logistics in Laekebeek (Brussels region), for which Inther Group was requested to design, construct and maintain the intralogistics system. This new warehouse (with a storage capacity of 25,000 m2 and several temperature zones) has now been put into use for storing and delivering medicines to more than 45 Belgian hospitals, doctors, pharmacists, and wholesalers. Incidentally, the building has also become the winner of Logistics Building of the Year 2022. Inther Group has provided the intralogistics hereof and integrated two former DHL sites into the new system at the new location.
Automation increases efficiency
Max Nijssen, the responsible Sales Engineer at Inther Group for this project, explains: “A major advantage of this project was that we could build it in a greenfield environment from the ground up at the new DC location in Laekebeek. This benefited the speed of construction and its final result. DHL was looking for higher efficiency through more automation to handle their order profile (delivery within 24 hours with higher numbers per order line) quickly and without errors. In addition, from a sustainability point of view, DHL wanted to be able to combine different orders from an end customer in one box. The complete and hybrid solution, therefore, consists of multiple elements, which together ensure the best result for DHL.”
For example, a shuttle aisle with 27 levels is used, of which 17 will be taken into use in the first period (± 6,500 stock totes). The shuttles have been equipped with Inther’s own DTS software for even better coupling and integration with all other hardware. 635 meters of Inther conveyor equipment lead to, among other things, four Goods to Person workstations with pointer lights for up to eight compartments per tote and Pick to Light solutions. An Inther ADI (Automated Document Inserter) ensures the correct documents in every shipment. A box erector and closer, three Print & Apply machines, and weighing scales complete the system for DHL – all in DHL’s own branding by the way.
Go-live is just the start
After completing various extensive test phases with hundreds of test scenarios and almost 1,000 actions at and by Inther Group and DHL (including a System Integration Testing – the link with the DHL system Gaels), the system was successfully taken into use by DHL in November 2021. In the aftersales phase, Inther Group will further analyze the process in real life in order to continue to optimize the system to the changing intralogistics needs of DHL and its customers.
DHL responds with satisfaction after go-live: the picking process is now much simpler, more efficient, and less stressful, as the goods come to the operator instead of the other way around. This was therefore enthusiastically received by the employees, but also offers advantages for the end customer. The storage is much more compact and the whole system offers several economies of scale, making it easier to expand to grow along with pharma customers. In addition, every step in the process is tracked, which ensures higher accuracy and traceability of all goods.
Inther Group is certainly very proud of this project and of the successful result and looks forward to a good and lasting cooperation with DHL.