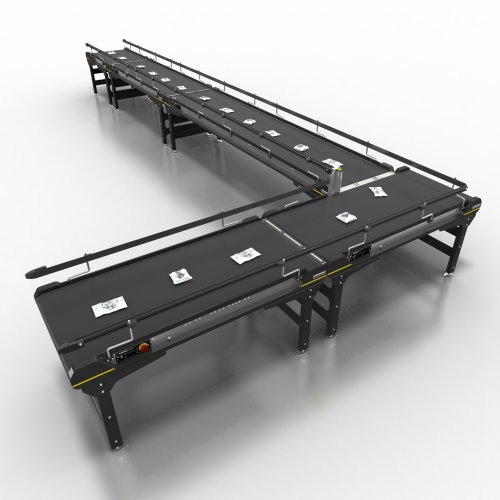
Interroll presents new plug-and-play conveyor platform for automated production environments
With the new Light Conveyor Platform (LCP), Interroll is expanding its range of products with a platform-based material-flow solution that significantly increases the productivity of manufacturing processes. Designed as a plug-and-play modular system, the LCP allows all system integrators to implement scalable belt conveyor sections very easily in order to quickly meet customer-specific automation requirements for material flow. The high quality and availability of this solution are ensured by, among other things, the use of technical products that have already proven themselves hundreds of thousands of times with users worldwide.
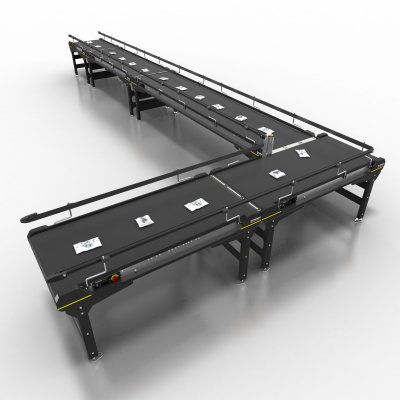
Interroll’s Light Conveyor Platform (LCP) is designed to transport smaller conveyed goods, as well as boxes or polybags weighing up to 50 kilograms.
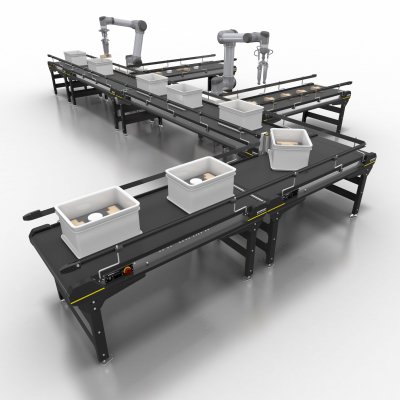
Interroll’s LCP offers perfect conditions for decisively increasing the productivity of production cells as well as assembly and packaging stations through efficient material feed and discharge.
Efficient material feed and discharge play a crucial role in realizing the productivity potential of manufacturing cells, assembly, and packaging stations. At the same time, rapidly changing process environments in many other industries require flexible conveyor solutions that can easily adapt to new requirements. This is what the Interroll’s new material flow solution for system integrators and plant engineers achieves: Corresponding LCP-based belt conveyors can be easily assembled from factory-preassembled and predefined modules without any engineering effort, and can be put into operation quickly and safely via an autonomous machine control system, optionally without an additional programmable logic controller (PLC). Depending on customer requirements and application, however, connection to an external PLC with user-specific programming is also possible.
Interroll’s LCP is designed to transport smaller conveyed goods, as well as boxes or polybags weighing up to 50 kilograms. The conveyors, which can also handle inclines or declines, are driven by compact and energy-efficient drum motors that have an efficiency of over 85 percent, keeping energy consumption and energy costs very low. The fully modular system can be planned and assembled very easily and conveniently on the PC monitor using Interroll’s popular Layouter tool. This drastically reduces project lead times and the necessary effort for system integrators. In addition, the predefined module sizes in different lengths and widths create the best conditions for fast production and delivery times.
During the development of the new platform, great importance was also attached to maximum workplace safety and a pleasant working environment. The new LCP was extensively tested before market launch, subjected to extreme endurance and load tests, and developed according to Design for Manufacture and Assembly (DMFA) standards. It features an integrated emergency shutdown at the push of a button, complies with all relevant safety regulations, and has a quiet noise level during operation.
The LCP is produced at Interroll’s site in Hvidovre, Denmark, and is available immediately in Europe, and soon in Asia and the Americas.