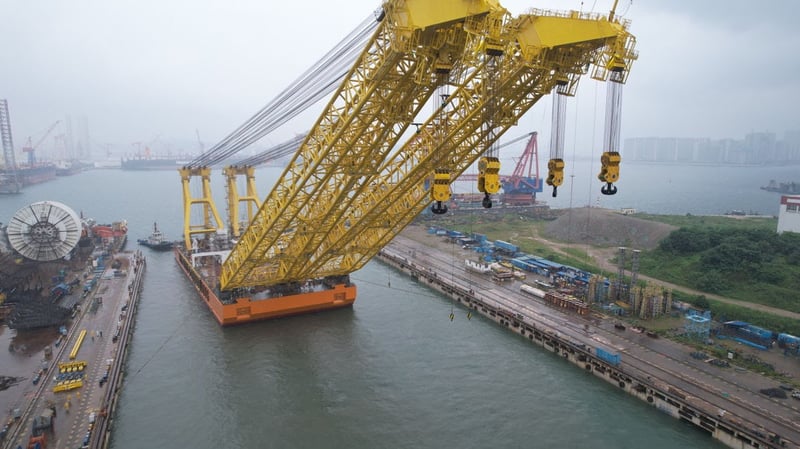
CP&A and DHHI partner on Hulking Offshore Crane
Casper, Phillips & Associates Inc. (CP&A) has completed a structural design review on a mega 3,500-tonne capacity double boom offshore crane.
CP&A—the company offers a wide variety of services, including procurement, specification, modification, and accident investigation—accepted a scope of work to deliver a structural review and design assistance from China’s Dalian Huarui Heavy Industry Group Co. Ltd. (DHHI). CP&A was challenged with finding a solution for increasing the strength of certain design elements.
DHHI recently completed manufacture; each crane boom, which sits side-by-side at the front of the vessel, can lift 1,750 tonnes. They measure over 128m—longer than a football pitch—and will be used both singularly and in pairs. The height of the crane mast, meanwhile, reaches 40.5m.
These mammoth dimensions allow DHHI’s crane to handle cargo as large as 32m-high, with a 50m by 50m footprint, over water or on land. Similar cranes, which will typically have a captain and a crane operator, have been used to erect dockside or quayside cranes and bridges, and in offshore applications, such as wind farms or oil rigs.
CP&A analyzed the crane and reported the reaction forces at the crane boom pin connections so that a foundation could be properly designed. Similarly, it reported the reactions of the mast ends attached to the barge deck under various load cases, extracting information for ship designers, so they could design for the required strength. There were a lot of different load combinations and scenarios that needed to be considered, such as different boom angles, wind, wave motions, etc. The lattice boom required many connection checks.
A complex project
Richard Phillips, a mechanical engineer at CP&A, said: “The analysis was rather complex; we had to use a special pipe-to-pipe connection post-processor that we created in-house.”
He explained: “Pre-processing is the creation of the mathematical model of the crane structure [defining structural beams, developing loads and load cases]. FEA processing is when you take the math model and solve it to get the forces in each structural member [beams and columns]. Post-processing is when you take the forces in each structural member end and check to see if the structural members and connections have adequate strength and resilience.”
CP&A’s stress program takes the forces from the finite element analysis and automatically checks the stresses of each member based on the specified design code. CP&A’s connection program takes the forces from the stress calculation results and checks the stresses of every pipe end connection according to the structural welding code AWS D1.1 for every single load combination.
Project execution required collaboration between Chinese and Pacific Time zones, with Mike Zhang, the chief mechanical engineer at CP&A, able to communicate in fluent mandarin where necessary. Phillips said that Zhang was the lead engineer on the project, which was especially useful when certain norms, guidance, metrics, and phraseology were used in the dialog. In fact, CP&A frequently works with Chinese companies.
CP&A has a long-running relationship with DHHI, notably collaborating with it on the crane base anti-seismic isolation system (BASIS), which is a revolutionary seismic isolation system built on nonlinear time history analysis (NLTHA). BASIS can protect a crane’s main structure from damage, even in contingency-level earthquakes.