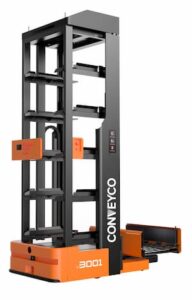
Conveyco’s new Flow Rack reduces labor and increases accuracy
Conveyco’s new flow rack Autonomous Mobile Robot (AMR) replenisher, the Stacker-Bot, allows organizations to eliminate labor and increase accuracy and efficiencies around the clock without the need for breaks or human supervision. The Stacker-Bot system can be integrated with flow rack, rack, shelving, conveyor and AS/RS workstation interfaces for both pick-ups and deliveries
Conveyco‘s new flow rack Autonomous Mobile Robot (AMR) replenisher, the Stacker-Bot™, allows organizations to eliminate labor and increase accuracy and efficiencies around the clock without the need for breaks or human supervision.
The Stacker-Bot can store and retrieve on a single trip up to five cases or totes. It can retrieve inventory from the floor, shelf or a conveyor level. The AMR continues to pick up to five SKUs for one trip. It automatically picks a case or tote, scans the barcode and stores it in the Stacker-Bot on any of the five onboard shelves. It then uses its RCS (robot control system) and communicates to the WMS/WCS host software system.
Once up to five totes or cartons have been retrieved in the Stacker-Bot, it is directed via the WMS/WES software host the exact locations required to place the inventory. The rack, shelf level and shelf location for each of the five SKUs is communicated to the Stacker-Bot. The robot always travels via the shortest path to its put-away location.
After the AMR has picked up the product to be replenished, the Stacker-Bot uses its two-dimensional camera technology to find its first location. It verifies its position by scanning the barcode on the rack and shelf level. Then, it automatically places the tote or case in the proper SKU location in the back of the flow rack. This operation is done transparently from the picking operator located at the front of the flow rack.
The Stacker-Bot travels to its next location and repeats this process until its load is depleted. It then goes back to the re-loading station to pick up more SKUs and repeats the process. Multiple Stacker-Bots are used to meet throughput and capacity requirements.
Each AMR is in communication with the WMS/WES/WCS software system. The Stacker-Bot can pick and stack up to five levels high or 102″ tall. Its total capacity is up to 500 lbs. per unit or 110 pounds per shelf level. The system travels of up to 1.64 feet/second via the shortest path to expedite its pick-ups and deliveries. Likewise, the totes or carton sizes can range from 15.75″ to 23.6″ X 15.75″ X 3.9″ to 12.2″ in size.
Because the Stacker-Bot is autonomous, it can operate without humans throughout the work area. Each Stacker-Bot comes equipped with multiple and redundant safety protection including a laser obstacle avoidance system to provide worker safety.
The Stacker-Bot system can be integrated with flow rack, rack, shelving, conveyor and AS/RS workstation interfaces for both pick-ups and deliveries.
“The Stacker-Bot Autonomous Mobile Robot replenishes and transports inventory to and from flow rack, shelves and workstations 24-7-365. This allows organizations to focus their scarcest resource, labor, in areas of the facility which provide the greatest value,” says Ed Romaine, VP Marketing.
The Stacker-Bot is just one model from the ConveyGo AMR and Robotics line available from Conveyco Technologies.