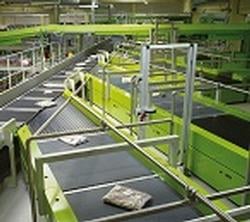
BEUMER presented its Belt Tray Sorter with various modules in action at CeMAT
The BEUMER Group recently presented a type BS 7 BT belt tray sorter, around 40 m in length, in action at CeMAT, the world’s leading intralogistics fair. The system was equipped with various modules and functions – such as the manual loading station, semi-automatic induction with camera system and a demo module of the BEUMER Warehouse Control System. With this, the intralogistics specialist demonstrated how it can provide efficient sorting systems to meet the demanding requirements of its customers.
In Hanover, the Beckum-based company presented the BEUMER Sorter BS 7 BT with a smallest possible separation of 400 mm. For special use at CeMAT, BEUMER had defined a speed of 1.75 metres per second. This means that the system reaches a sorting output of 15,750 items per hour. At the maximum speed of 2.5 metres per second, the machine capacity increases to 22,500 items per hour.
For around 15 years now, BEUMER has been using contactless power transmission instead of the normal conductor lines for its sorters. As a result, users can reduce the need for machine maintenance and replacement parts to a minimum, and also avoid the dust that occurs with conductor lines. At the exhibition, the sorter was fitted with the innovative OptiDrive friction wheel drive which BEUMER has developed and patented. With an efficiency of up to 80 percent, this innovative drive system is particularly energy-efficient and durable.
From the manual loading station to the camera system
To show visitors how BEUMER can meet the individual requirements of users in the best possible way, the specialists equipped the sorter with various modules and functions. These included a manual loading station, which offers a cheaper option for inducting goods onto the sorter. Because the operator places the goods manually onto a sorter tray, he can assess the product again before the automatic sorting process. If he sees that the product is damaged, he can remove it from the sorting process in good time. Because manual loaders can be set very flexibly and users can react quickly to performance peaks, these solutions are particularly popular in industries with high peak phases. At the trade fair, the specialists showed that the manual loaders can also be installed in curves, which means that these sorter sections, where there are normally no functions, can also be used effectively. This considerably improves the system’s commercial viability.
Another option for taking the goods to be sorted as bulk products to the sorter is semi-automatic induction. This works on a similar basis to the manual loading station. While the employee places the items onto the conveyor one by one, he can also check the condition of the goods before they are taken to the automatic sorting process. The advantage over manual loading is that the operator can work independently of the sorting speed, because the products reach the sorter via the induction unit. With this dynamic process, the system measures the items and determines their position. The information is forwarded directly to the control process so that the products are placed optimally on the belt tray element. This increases precision when the items are discharged and helps to avoid errors on the part of operators. The system, for example, detects items that are overlapping. The induction stops and the operator can correct his mistake.
Another module is the camera system which reads barcodes on the products as they are being inducted. If the system does not recognize the barcode, the product is not forwarded. Time-consuming no-read handling can thus be reduced or completely eliminated.