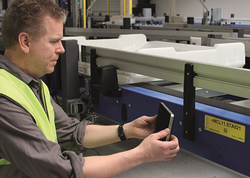
BEUMER Group develops smart maintenance system for customer support
Augmented reality offers interesting possibilities and potentials, e.g. for maintenance work on intralogistic systems: a head-mounted minicomputer could display all necessary information to the service employee. This would simplify their work, hands-free. The BEUMER Group development department places a high priority on this topic. With an app for smart maintenance on mobile end devices, our customer support technicians can quickly access all important data.
Companies must repair their machines and systems quickly to avoid costly downtimes. This is becoming a more difficult task as systems are becoming increasingly complex, requiring highly qualified service technicians. Even the most skilled technicians sometimes have to read through heavy manuals, open up drawings or struggle with outdated plans. This costs valuable time, and should be so much easier in the digital age. Tablets, smartphones and smartwatches have become indispensable in our private lives. Even smartglasses are increasingly finding their way into our lives. A tourist strolling through Paris, sits down at the Eiffel tower, puts on his glasses and gets all the information he wants, according to his location and true to scale: How tall is the building? What are the opening hours? How did these scene look like 100 years ago? “We take up this technological trend, to complement reality with digital information,” says Dr. Andreas Werner, head of the research and development department with BEUMER Group. “This app for smart maintenance will help facilitate maintenance work on intralogistic systems for BEUMER Customer Support employees.”
App facilitates maintenance
Through AutoID characteristics on the logistic element, e.g. a conveyor, and the smart maintenance app, information on this element can be displayed, such as maintenance instructions or pin assignments. The service employee focuses on the object with his mobile device. The required data is displayed on the live image of the camera of the device. “The technician looks at the defective part and can immediately call up every related manuals or goods in stock, ” explains Dr. Andreas Werner. Every process step is displayed. In the event of very complex processes, he can call a colleague by using the smartglasses and solve the problem together via live stream. Measured values could be recorded at the same time and transferred to the back-end system in real time. Video recordings and photos can document whether an order was carried out correctly and in compliance with the safety regulations.
Smartglasses, tablet or mobile phone?
“When implementing these wearable computer systems into intralogistics, you have to consider aspects like information security, ergonomic user interfaces and suitable IT structures,” explains Dr. Andreas Werner. The goal is to ensure a sustainable added value for companies and customers. But which mobile end device is the most efficient? The app can be used on smartphones and tablets for example. They offer the advantage of a high computing capacity. This allows you to process the large amount of data that is required for service tasks. Their interfaces are standardised and always have direct access to the Internet. Their handling is intuitive and easy. One big advantage: these devices are accepted technologies at the workplace because they are already indispensable in our private lives. Smartwatches, however, have a low computing capacity , their interfaces are sometimes specific to the manufacturer and the user requires additional devices. Smartglasses are also very easy to use and their interfaces are standardised. Their availability however is still too low for industrial applications. As with smartwatches, the user requires additional devices. Smartglasses have many operating advantages, but they are still not developed enough to make an industrial use possible.
Smart maintenance at Singapore airport
“Tablets are already used at several airports that operate baggage handling systems from BEUMER Group,” describes Dr. Andreas Werner. This includes Singapore Changi Airport. As one of the main hubs for Southeast Asia, this airport is known to be very progressive and passenger-friendly. The baggage handling system was developed and integrated by BEUMER Group. BEUMER Group is exclusively responsible for ensuring trouble-free operation, optimum maintenance and therefore the long-term coordination of the baggage handling systems. This is why 121 employees take care of customer support. They provide 24/7 operation at the baggage control rooms and necessary preventive maintenance to ensure continuous system availability and best performance.
“The maintenance personnel can use the tablets to connect to individual system control components to check for example statuses or carry out modifications,” says Dr. Andreas Werner. BEUMER Group employees can scan barcodes from components and look into further data, such as maintenance protocols, using the integrated camera. Maintenance and repairs are carried out a lot faster, and system standstills are reduced. This ensures reliable operation and reduces costs.
Developers are currently carrying out an innovation study with the smartglasses at the airport. The employees receive information on the system layout in 2D via their device, the error history, or device-specific information, and gets VoIP access to customer support. They can access operating and maintenance instructions easily and quickly. All of the information necessary for troubleshooting the system is available. The device can also be connected to the smartphone via Bluetooth.