
ALPS Inspection introduces BottleStop™ Multi-Head Leak Tester
ALPS Inspection is the global industry-leading manufacturer of non-destructive, in-line leak inspection equipment for empty plastic containers of all sizes, shapes, and materials. Today, ALPS Inspection has announced the launch of its new BottleStop Multi-Head Leak Tester. BottleStop offers unmatched versatility and reliability in a streamlined, cost-effective solution designed to meet the evolving needs of blow molding manufacturers.
BottleStop is tailored for manufacturers producing angle neck, choked neck-prone, and large, stable containers. With enhanced capabilities, including angle neck testing and advanced control systems, it delivers the performance and precision required for today’s quality control standards.
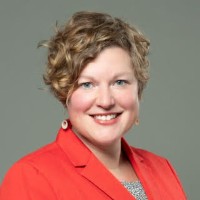
Jill Shearer
“Our customers face increasing demands for efficiency and precision in their production processes,” said Jill Shearer, General Manager for ALPS Inspection. “BottleStop addresses these challenges by ensuring controlled container handling for tricky applications. It’s not just a leak tester—it’s a streamlined solution that meets a specific market need.”
BottleStop integrates seamlessly into existing production lines, requiring minimal modifications saving on floor space. Its flexible design supports various container types and configurations, making it an ideal solution for a wide range of industries, including household, industrial, and automotive applications. Capable of inspecting up to 65 containers per minute, BottleStop combines speed with precision.
Key Features of the ALPS BottleStop Multi-Head Leak Tester include:
- Multiple configurations: Inspects up to 65 containers per minute in 2-, 3-, or 4-head configurations.
- Testing probe adaptability: Switch between angle neck and standard neck applications with an optional choked neck probe available.
- Seamless integration: Mounts over the existing conveyor system with no major modifications required.
- Compact design: A small footprint allows for easy implementation in space-constrained production environments.
- User-friendly controls: Features a full-color HMI touchscreen with data graphs and reports for efficient process monitoring.
- Automated performance: The gate cylinder regulates container flow, while programmable sensors ensure precision in testing and defect rejection.
BottleStop is equipped with ALPS’ latest technology that optimizes production performance while maintaining stringent quality control standards. It provides valuable features such as a self-test function to verify system calibration and ensure reliable detection of even the smallest defects.
“With BottleStop, manufacturers can confidently meet today’s quality demands and prepare for the challenges of tomorrow,” Shearer added. “This system is designed to support ongoing product innovation and deliver consistent results, making it a vital tool for many production lines.”
BottleStop is ideal for HDPE containers produced through the Extrusion Blow Molding (EBM) process, including products such as household toilet bowl cleaners, industrial chemical containers, and automotive fuel additive containers. With its flexibility and adaptability, BottleStop is a valuable asset for manufacturers seeking a reliable, streamlined leak detection solution.