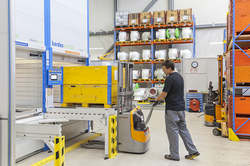
ABB Schweiz integrates new Shuttle XP 1000 for pallet storage
The power and automation technology group at ABB Schweiz has been using storage and retrieval solutions from Kardex Remstar in its Oerlikon site for quite some time. Recently, ABB ordered two Shuttle XP 1000 Vertical Lift Modules (VLMs) to store full pallets. Performance in the tool warehouse has improved even further since.
ABB employs around 6,500 people in Switzerland and focuses on the power and automation technology divisions. Gas-insulated switchgears for grid power distribution are manufactured at the site in Zurich/Oerlikon. The assembly tool pool supplies tools and materials for assembling new switchgears as well as spare parts for servicing and maintenance. About 1,000 different items are stored in the warehouse and around 8,000 in total.
The tool pool has been storing its materials in storage systems from Kardex Remstar for quite a while. Twenty VLMs and vertical carousels have accumulated over time as a result. The units have also survived a few location moves, both from one facility to another and within an existing building. ABB began with two, 16 foot tall VLMs. At the time, there was an option to add to these if necessary – this was an important argument for ABB to justify investing in automation in the first place. The VLMs are now almost 30 feet tall and make optimal use of the building height. Beat Rutishauser, head of the assembly tool pool, and his team refer to the collection of storage systems as “Our Little Manhattan”.
The individual tools and materials for the assembly sets are stored in multiple Kardex Remstar VLMs and are retrieved at the touch of a button. Incomplete assembly sets used to be stored on pallets in static shelving, creating a bottleneck which gradually led to a shortage of storage space.
“Little Manhattan” has grown since the beginning of 2015. Two of the new Shuttle XP 1000 units measuring almost 30 feet tall are being used for pallet storage. Pallets with semi-picked tool sets wait in one unit as buffer storage until all of the items are available to complete the set. Once the set is ready, it is conveyed to the shipping department and sent to ABB locations around the world. “It is essential that the assembly sets arrive at their destination on time, wherever that may be in the world. It is the only way in which the systems can be built on schedule”, says Rutishauser.
With a maximum tray capacity of 2,204.62lbs (1,000kg), ABB is taking advantage and storing almost full capacity at 2,094lbs per tray. Based on the goods to person principle, the pallets are brought directly to the operator at an ergonomic height. Then the pallets are moved into position to be picked up by a forklift or electric pallet truck with the help of a tray extraction device. The pallets are lowered into specially designed trays for storage. At ABB in Oerlikon, it must be possible to not only store two pallets next to each other, but also pallets with a double frame, which means the height of the stored goods is around 3 ft high. Both VLMs have space for 58 pallets and occupy a footprint of only 204 square feet.
ABB Schweiz utilizes these two VLMs anywhere from 20-50 times per day. Using these modular storage systems has helped ABB save space and increased productivity within their existing warehouse.