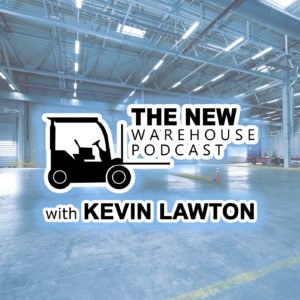
Episode 561: Maximizing profits with fewer robots – The breakthrough from Zebra Robotics in AMR Utilization
On this episode of The New Warehouse Podcast, Kevin is on-site at Zebra Technologies’ robotics demo center in San Jose, California. He’s hosted by Cody Upp, leader of Zebra’s commercial organization, and Achal Arvind, Director of Robotic Solutions. Together, they explore Zebra’s latest innovations in warehouse automation.
Zebra Technologies is a well-established leader in supply chain solutions. With the acquisition of Fetch Robotics, it has taken a focused leap into robotic automation. Its latest fulfillment-focused solution, Zebra Symmetry Fulfillment, introduces a game-changing approach: decoupling autonomous mobile robots (AMRs) from carts. Tune in to hear how this creates a more efficient, cost-effective system that reduces reliance on excess robots while enhancing productivity.
Unlocking Efficiency: Why Zebra Robotics Focuses on Fulfillment
Zebra’s robotic evolution stems from years of experience in supply chain automation, but now, they are taking a hyper-focused approach to fulfillment efficiency. Unlike general warehouse automation, Zebra has narrowed its focus to fulfillment workflows, where the most immediate impact can be made. “The business pains that our customers are seeing… there’s a tremendous disproportional amount of labor continuously being spent on what we categorize as the each picking function,” says Upp.
For instance, the labor-intensive process of fulfillment—where workers spend excessive time walking, searching, and retrieving goods—presents an enormous opportunity for automation. By refining their solutions specifically for this segment, Zebra Robotics is streamlining workflow execution, reducing walking time, and increasing operational efficiency.
Arvind emphasizes that this transformation was intentional: “We took a lot of the learning from being in a lot of different environments and applied that to build a system that’s focused purely on fulfillment, that’s solutions driven.” This narrowed focus has allowed Zebra to develop an ecosystem tailored to fulfillment challenges, making automation more precise, efficient, and cost-effective.
Decoupling AMRs: A Game-Changer in Warehouse Robotics
One of the most groundbreaking innovations Zebra Robotics has introduced is the concept of decoupling AMRs from carts. This strategic shift significantly enhances warehouse efficiency. Instead of requiring AMRs to remain attached to carts throughout the process, Zebra’s approach allows carts to be staged separately, freeing AMRs to focus on transportation rather than waiting idly at induct and packout stations.
Upp explains, “Fewer robots, greater profits. If we can hit design levels, if we can hit performance rates, and operate with 30% fewer robots while maintaining a competitive cost structure, that is the recipe for greater cash flow on these investments.”
The decoupling process reduces AMR downtime, eliminates bottlenecks at induction points, and ensures continuous movement of both human workers and automation. As a result, fulfillment centers can operate with fewer AMRs while still increasing overall throughput.
Consequently, this innovation is particularly valuable given the industry-wide shift toward maximizing cost efficiency. As Upp notes, “Fast-forward to 2025, and CFOs are looking for meaningful financial investments that are going to impact the bottom line.” By focusing on AMR utilization rather than simply adding more robots, Zebra is reshaping the way warehouses approach automation.
Team Intelligence: Optimizing Human and Robotic Collaboration
A key aspect of Zebra’s fulfillment solution is its Team Intelligence system, which optimizes the interaction between human workers, AMRs, and carts. Unlike traditional zone-based picking methods, where operators wait for work to come to them, Zebra’s system takes a different approach. It ensures that tasks are continuously assigned based on real-time location and operator availability, keeping the workflow seamless and efficient.
“At the heart of what we were trying to do with Team Intelligence is as a picker, you always know what you’re doing next, and what you’re doing next is as close to you as possible,” says Arvind.
This system minimizes unnecessary walking and eliminates downtime, directing workers seamlessly from one task to the next. By digitizing both robots and human workers, Zebra Robotics provides real-time insights into warehouse operations, optimizing labor efficiency while maximizing order throughput.
Upp adds, “There isn’t a solution out there today that is equipping operators with a digital agent, with a wearable… The idea that we aren’t directing a workflow at all times through a building is almost nonsensical.” By ensuring continuous task allocation and reducing inefficiencies, Team Intelligence sets a new warehouse automation standard.
Key Takeaways
- Decoupling AMRs from carts increases robot utilization and reduces idle time, allowing warehouses to operate with 30% fewer robots.
- A fulfillment-focused approach targets the most labor-intensive processes, precisely addressing industry pain points.
- Team Intelligence optimizes workflow, ensuring pickers always have a directed task, reducing unnecessary movement.
- Cost-efficiency and accessibility are priorities, with Zebra leveraging standard warehouse carts and reducing infrastructure requirements.
- Data-driven decision-making enhances warehouse visibility, enabling managers to track real-time operations and maximize efficiency.