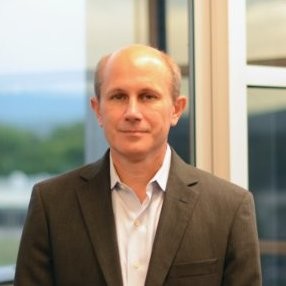
Why you’re waiting longer for a forklift – and what to do about it
While the COVID-induced supply chain backlog is loosening up, not all warehouses have been able to return to normal – especially if they’re in the market for new materials handling equipment.
Businesses looking to purchase new forklifts in particular are being quoted some eyebrow-raising lead times. Electric forklift lead times are running close to normal, about 35 weeks, but internal combustion forklifts, which would usually take 25-30 weeks, are taking 40-45 weeks. Perhaps the most astonishing wait: narrow aisle equipment, which often takes about 35 weeks, might take two years to arrive according to Kenco Group data. This logjam has led to soaring prices and headaches in the warehouse, as managers try to maintain their current fleet as long as possible.
Here’s a look into the factors that are causing the shortage, what to expect in the coming months, and how to navigate the shortage while continuing to meet customer demand.
What’s lifting wait times?
Supply chains might assume that COVID is the culprit – and they’d be partially right. But that’s only scratching the surface. There are actually four factors that are contributing to the longer lead times:
- The COVID Shift. Consumers were already relying heavily on e-commerce prior to the pandemic, but purchases via digital storefronts skyrocketed in 2020. As warehouses rapidly replaced physical stores as the last touchpoint before the customer, warehouses began ordering additional forklifts to meet demand.
- The Chip Shortage. As forklift manufacturers tried to keep up with demand, they ran into a different backlog – microchips – slowing down the process even more. And with demand rising for electric vehicles, there is greater competition for the precious few microchips, making this backlog far from fixed.
- The EPA Violation. In early 2021, the EPA announced Toyota – the parent company of Toyota Material Handling, Inc., a forklift manufacturer – had been non-compliant with EPA reporting guidelines around emissions-related defects. The fallout rippled across Toyota’s businesses, and because Toyota Material Handling struggled to obtain engine emissions certifications later that year, production was temporarily halted. It has since restarted, but the manufacturer is still catching up on orders.
- The Big Buy. Here’s why narrow aisle equipment is taking so long to arrive: a major e-commerce company recently placed a sizeable order, in the tens of thousands, for new trucks – something that wouldn’t typically complicate the supply chain, but has been magnified because of COVID and Toyota’s manufacturing challenges.
What will this cost me?
The scarcity of materials to manufacture forklifts, compounded by inflation, means the forklift backup will likely give your wallet headaches as well. The cost of a new forklift is up about 27% from two years ago, and used forklifts have almost doubled in price. And as the Fed continues to fight the 8.3% inflation rate by raising interest rates, a forklift lease will currently involve a 7-7.5% interest rate, up 3-3.25% from normal.
Inflation has had a significant impact on all areas of the forklift manufacturing process, from wages to raw materials. Steel, copper, and lead are particularly expensive at the moment; lead, which is especially important in the development of microchips for electric forklifts, has gone up in price because of U.S. tariffs on raw materials imported from China.
How Do I Respond?
Unfortunately, it’s likely warehouses – especially those looking for more specialized equipment – aren’t going to see resolutions for these challenges in the near term. It’s important for warehouse managers to closely maintain their current fleet while they wait for their new vehicles. That means preemptively buying various replacement parts well in advance, as these parts will also be in high demand.
The best option for fulfillment centers is to closely monitor the utilization of their equipment. Different forklifts can run for varied cycle lengths before they need significant maintenance; keeping track of these timeframes can ensure warehouse managers perform maintenance in the correct cadence and optimize the forklift’s life expectancy. Alternatively, warehouses can invest in telematics software that will keep track of forklift utilization automatically, taking any guesswork out of when forklifts should be serviced.
What’s Next?
While new developments such as the Chips and Science Act, which increases U.S. investment in microchip manufacturing, could help ease some of the forklift backlogs, its likely warehouses will continue to endure long lead times and higher prices throughout 2023. That’s why due diligence with existing forklifts will be critical for warehouses and distribution centers looking to weather the shortages. With a combination of proactive maintenance and advanced software, supply chain managers can ensure the most efficient use of their equipment on hand.
About the Author:
Allen Polk is the Vice President of Sales for Kenco Group, with 20+ years of experience in sales and business development in the material handling industry. His responsibilities at Kenco are managing day-to-day sales operations and client relationships, technology development and integration and white label product management. From the beginning, Polk has always had a passion for creating meaningful client relationships, supporting team members and earning success for his clients. Prior to Kenco, Polk worked at Caterpillar in sales and business development. He attended Mercier University, receiving his Bachelors in Business Administration.