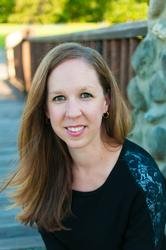
In pursuit of safety
Safety in the workplace is a goal offering numerous benefits. From aiding in worker retention and meeting standards to ensuring the best for employees, safety is one of the keys to an organization’s success.
New designs making an impact
One company that has been bringing its safety technology to the industry in recent years is seeing some positive results. HeroWear designs exosuits that aid workers in performing demanding movements at work, according to the business website. “It was born out of a research project at Vanderbilt University,” said Mark Harris, co-founder, and chief executive officer of HeroWear.
Dr. Karl Zelik, a biomechanical engineer, had experienced back pain from lifting two small children, according to Harris. “He thought, ‘Could I design something that would take the load off my back and wear every day?” said Harris, who said the concept led to several years of research and development at Vanderbilt.
Harris said as the project grew from the research phase, it was introduced to companies and interest was strong. The idea formed of providing a solution to a major industry problem, namely, back pain and injuries. A prototype was launched and HeroWear was formed, announcing the HeroWear Apex.
The exosuit is a flexible 3-pound suit that takes 75 pounds of strain off a back with every lift, according to the business website.
“For some users, it’s actually closer to 125 pounds of back relief,” the site said. The exosuit is designed to support and assist the lower back muscles involved in repetitive lifting and bending activities, according to the website. It provides strength by functioning with a patent-pending on-off switch, the site said.
The switch is “activated by a single, easy-to-use switch that can even be operated through personal protective equipment and coveralls,” the website said. HeroWear officials stress that the exosuit can be integrated with other types of safety equipment already in use. “It works fine on a pallet jack or a forklift,” Harris added. “This was important when we designed it.”
Today, HeroWear has over 200 customers, according to Harris. Many companies want to test a launch of the product on a subset of workers and then expand use, he said.
“Typically, we see companies start out with 10, 20, or 30 units. They will try them out on a number of workers,” said Harris, who said HeroWear works with its customers to ensure the Apex suits are sized per worker. “It’s really important that these fit very well or else you don’t get the biomedical advantage,” said Harris, noting that the exosuits are modular so pieces can be rebuilt for specific workers.
The anecdotal reports from users have been positive, according to Harris. “What we hear a lot of after the first week is, ‘I’m going home and I’m not sore anymore. I can play with my kids. I’m not collapsing on the couch,” Harris said. “That’s what gets us really inspired.”
The Apex 2, a redesign based on three years of research, was launched in mid-March, according to Harris. When working with a company, he stressed that HeroWear aims to learn more about how the operation functions. The company does recommend starting with more than a single exosuit. “There is a psycho-social aspect to this. You are putting something new on a worker. You need a critical mass of workers, so it becomes somewhat normalized,” said Harris, who said there is better success in a launch when several workers are wearing the exosuit.
Having equipment like the HeroWear exosuit on hand can possibly help with employee retention as well, Harris noted. “These are really, really hard jobs. It’s that first few weeks or a couple of months when they realize how hard it is. If you can make the job a little easier, a smoother transition, we suspect that will improve retention,” he said. The bands on the exosuits are replaced every 12 -to-18 months and the textile base has a 4-to-5-year life, according to Harris.
The company’s leaders imagine widespread use of the products in the future. “Our long-term vision is everybody has an exosuit in their garage. Like everyone has power tools. Maybe you don’t need it every day, but it’s there,” said Harris, noting that everyone needs to do some amount of lifting and leaning in their daily lives.
He added that research shows about 80 percent of the population will experience back pain at some time in their lives. “It’s kind of crazy that we lift things now in the same way as the people who built the pyramids. The physics haven’t changed,” Harris said. “It seems like a pretty big opportunity.”
Studying standards
For those looking to stay up to date on robotics, Jeff Fryman offers courses through the Association for Advancing Automation, or A3. “I go through an overview of the basic safety requirements from the American national standard, the ANSI / RIA R 15.06,” said Fryman, a safety standards trainer through A3. He said his courses cover risk assessments and task-based methodology consistent with what the standards require.
Class attendees are typically safety engineers or mechanical control engineers responsible for designing and implementing robot applications, according to Fryman. He also offers a class that is more in-depth on standard requirements.
Fryman teaches both in-person and online. He noted that the international safety standards match up with the national requirements and has had students around the world for the classes. “There’s basically one worldwide robot standard,” Fryman said. “We’re working on the basic industrial robot, not the walking, talking supermarket-greeting robots.”
The basic course is offered monthly and collaborative robot safety training is bi-monthly as a webinar on the A3 website at automate.org. For in-house classes, Fryman said he encourages a limit of 30 students in the room to enhance participation.
Although the course is geared toward the manufacturers and integrators of the robots, Fryman said he does address the topic of users in the training and the importance the standards have throughout an organization.
“If you have robots, you need to know about the standards for robot safety that covers them. It’s useful for the plant managers,” Fryman said. Industrywide, some safety dates coming up this year include OSHA’s Safe and Sound Week from Aug. 7 to 13, and ITA’s National Forklift Safety Day on June 12 and 13.
Industry award
Individuals are making advances in the name of safety as well. The American Society of Safety Professionals recently named Subba Rao Palagummi as the 2023 Safety Professional of the Year.
Palagummi, CSP, CMOISH, F.S. Eng, is an oil and gas industry safety expert who has helped advance occupational safety and health for more than 30 years in India, Kuwait, and the United Arab Emirates, according to an ASSP press release.
Palagummi is a corporate health, safety, and environmental specialist at Abu Dhabi National Oil Company (ADNOC), overseeing a large team of health, safety, and environment professionals and contractors, the release said. “He has built a reputation of being a safety leader with integrity, knowledge (and) ethics, the release said.
Palagummi developed and delivered a training module called “Supervising for Safety” and organized a successful road safety awareness campaign, according to the ASSP. “He has spearheaded task forces across the group and developed standards and guidelines that led to corporate performance improvement and an enhanced safety culture,” said Tahir Azhibekov, a health, safety, and environment manager at ADNOC. “His business acumen and people management skills are very much admired across the organization.”
Palagummi also mentors fellow safety and health professionals to help them advance in their careers, according to ASSP. He is a lead auditor, is known for his ability to work collaboratively, and is experienced at creating emergency response plans, the statement said.
Palagummi said it was a privilege to receive the award. “This is definitely a proud moment for me,” he said, expressing “sincere gratitude” to the ASSP leadership and board of directors. He thanked those who introduced him to the society and senior ASSP members supportive during his career.
“Special thanks to Mr. Ashok Garlapati who has been my mentor and extending his guidance and continued support,” Palagummi said. “This achievement would not have been possible without my ADNOC Onshore management support,” he added, noting the company’s HSE leadership for recognizing his efforts in various initiatives.
Asked about his work with students and guiding the next generation of workers in safety projects and careers, Palagummi said he feels it is “the need of the hour” to create interest and confidence in HSE as an academic choice and profession.
“The requirement to produce HSE professionals is very much essential to the industry and specific to oil and gas, chemical industries, and construction industries,” Palagummi said.
He noted that he regularly visits universities and conducts awareness sessions on HSE certifications and opportunities. “HSE professionals need to continuously engage with organization leadership to ensure they walk the talk to support HSE programs and initiatives which are aimed at improving the HSE culture,” Palagummi said.
Palagummi said every industry currently has an established set of HSE standards, procedures, and guidelines that are being effectively implemented. In the next few years, Palagummi said he hopes to see safety practices developed focused on proactive indicators like fatigue management, mental well-being, and well-defined mentoring programs. “Organizations also need to embrace the new environmental, social governance requirements to meet the current industry expectations as well,” he said.
About the Author:
Eileen Mozinski Schmidt is a freelance writer and journalist based in the Greater Milwaukee area. She has written for print and online publications for the past 14 years. Email editorial@MHWmag.com. If your company would like to be featured, email editorial@MHWmag.com