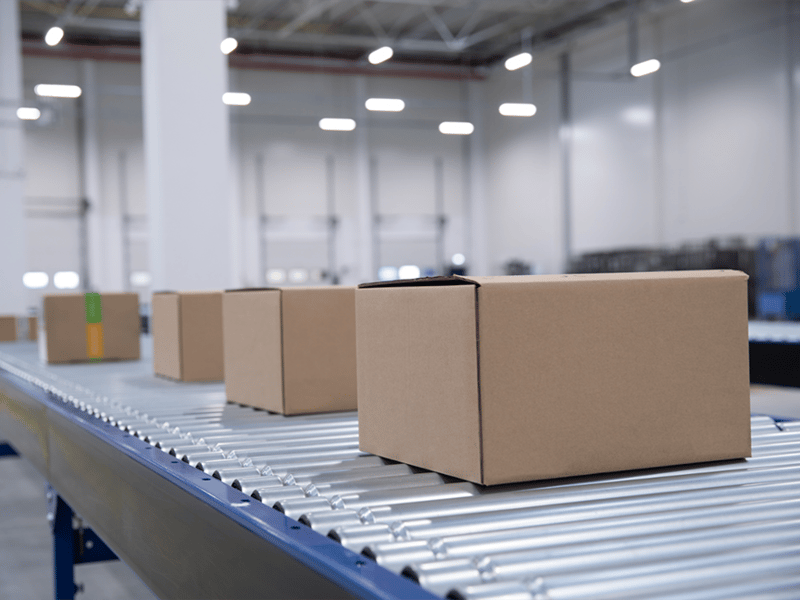
How technology enables the ‘Demand-Driven Enterprise’
What is a demand-driven enterprise? The Demand Driven Institute defines it as one that “can sense market changes, adapt to complex and volatile environments, and develop market-driven innovation strategies.”
At the same time, the demand-driven enterprise can’t ignore its execution arm — the warehouse. That’s where people are responsible for planning, yard management, warehouse management, and inventory control. They rely on data and systems to manage shipping, receiving, dock schedules, inventory control, labor planning, and work release, among other functions.
Most distribution centers have a number of complex tasks that are hindered by multiple constraints, as they struggle to get the right inventory out the right door at the right time. But technology can help them to make decisions faster, resulting in optimized warehouse operations and increased efficiency.
It’s not easy to identify a single point of failure in today’s complex supply chains. COVID-19 has led to raw-material shortages and missed production schedules. Companies overproduced during the pandemic, and are now facing the consequences of having used up much of their raw-material inventory. Meanwhile, in the warehouse, labor availability remains a big problem, prompting efforts to digitize and automate support systems. But delivery schedules for new equipment can be up to 36 months out. So most organizations are exploring innovation through software.
One of the first places warehouse managers look to drive value is visibility platforms, which help to determine where inventory is and when it will arrive. But given that they provide all this data, why is there still a shortage of toilet paper, chicken, and semiconductors in the market today? Who in the supply chain is really at fault? Production blames raw materials procurement and planning, while transportation blames production for not running to agreed-upon schedules. And transportation gets blamed when there aren’t enough trucks to deliver the goods. Finally, responsibility goes to the DC, which has been whipped around by upstream processes and can’t ship anything on time because trucks are showing up six hours late and there isn’t enough labor to run the DC.
To mitigate this whipsaw of blame, new systems must be introduced that provide rapid decision support and enable demand-driven execution. Execution platforms tie together visibility, the yard, enterprise resource planning (ERP), warehouse management software (WMS), and other systems. But to implement these applications successfully, management must be prepared to lose a portion of the manual control it’s used to.
For example, at one consumer packaged goods producer, the third-party logistics provider was given a full execution plan for the DC. It needed to receive the plan, review it, and manually enter cherry-picked components into the WMS, which directed workers to change their workflow. This took a massive amount of time and was almost worse than having no optimized plan to begin with. To reduce friction and drive execution, plans were pushed directly into the WMS. Once the team automated the decision-making process, efficiency increased by 200% overnight.
There’s much talk in supply chains today about the need for visibility, predictability, and prescriptive analytics. Yet few organizations are translating those capabilities into comprehensive execution plans. Even with artificial intelligence and prescriptive software, execution is needed to make everything work smoothly.
In an ideal world, all warehouse planning is on autopilot. The facility reduces the need for decision-making, eliminates bottlenecks, and allows key personnel to work with teams on the floor to increase productivity.
With automation, plans can be created and directly injected into the WMS. Planning time is reduced by 97%; productivity increases by 16%; inventory waste is reduced by 13%, and intra-campus transportation costs fall by 31%. In the process, demand can be met, production runs on schedule, inventory moves off the shelf, and orders are shipped to customers on time, in full.