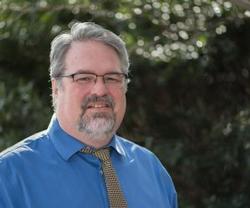
Forklift operator shortage affecting plants
Everything except the challenge is small at the MAU Skill School.
A forklift operator training course looks much like a driver education course, but more compact with cones and posts indicating the narrow lanes of factory floors. The sounds of small engines propelling the little vehicles is constant, punctuated by the sharp beeps of small horns — a cacophony that begins to fade away, but only for a moment.
“Stay on those horns!” an instructor shouts. He wants to make sure it’s ingrained in these students. Safety is more important than anything, they’re told, even more than precious cargo.
So even on this course of a make-believe factory floor, where people and equipment are indicated by pylons and cones, the students push their horn buttons anytime a make-believe person can’t see them around a pretend corner or anytime they change directions in the stout little machines that move materials around the world’s factory floors.
What looms large for MAU’s Jared Morgan is the need this course is struggling to satisfy. The tight labor market has been good for the best employees at Upstate plants. It’s given them opportunities for advancement, but many of them have advanced out of the forklift operator field to other positions, and the pool of operators hasn’t been replenished at a pace to keep up with demand.
“The shortage of qualified forklift operators is great,” said Morgan, director of recruiting and staffing for MAU. “Data suggests that there are hundreds of unfilled forklift or material handling positions in the Upstate of South Carolina alone. With so many employers needing skilled operators to navigate their busy production floors it has been very difficult for them to secure talent long term since qualified job seekers have so many great opportunities.”
The MAU Skill School was launched to provide at least one solution. It’s a training ground for employees hired by MAU as well as for lift operators already in place who need additional training. Morgan said the market needs them faster than they can cycle through the program. He meets weekly with plant executives to assess their needs and how those needs match up with qualified lift operators.
“Several factors play a role in the shortage, from what type of equipment candidates have experience with to the environment and pace of work they have experience operating in,” Morgan said. “The pool of qualified forklift candidates just isn’t growing at the same rate as the manufacturing needs.”
With deep roots in human resources, MAU didn’t want to simply hire people to operate forklifts, the company wanted to hire them and make sure they were properly trained for the jobs, with that training including a heavy emphasis on safety. The skill school was created at a site off Highway 101 in Greer. They offer training for beginners and experienced operators, some of whom will be MAU employees but contracted to work in plants.
“We train individuals who do not have experience and some who have decades of experience,” Morgan said. “We teach safety principals, proper lifting techniques and how to operate different types of powered industrial equipment.”
Students who complete the program will expect to earn anywhere from $12.50 to $22 an hour, depending on what other duties are associated with their jobs, Morgan said.
“Forklift opportunities are generally for more experienced (workers) with some other manufacturing experience. In most cases career forklift operators started off performing well in other manufacturing roles and were provided an opportunity to learn how to drive a lift and then decided to make a career out of it,” Morgan said. “Many forklift operators really enjoy what they do and have made very successful careers out of driving a lift.”
Some innovations in materials handling have had small impacts across industries, but Morgan said even the most advanced plants still count on lifts to get the job done.
“The demand and shortage for qualified drivers is spread across all segments,” he said. “If a company needs material moved from point A to point B then they are likely feeling the impact of the shortage in some way. Since almost all manufacturers need material moved, and forklift operators have been the traditional means of doing so, many if not all are negatively impacted by the shortage of drivers. This means many manufacturing companies can feel at least some impact to their supply chain.”
The typical training programs last 10 to 70 hours, depending on the need, and candidates are assessed for skill level.
Reach Ross Norton at 864-720-1222.