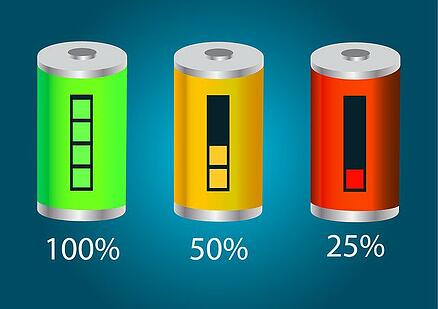
Why invest in battery monitoring?
There are probably several things you could do to improve inventory movement and boost your facility’s bottom line, but battery monitoring might be the easiest one to implement and generate the greatest results.
Battery monitoring technology is an investment that pays off because it easily lets you drive efficiency by monitoring your batteries, the charging habits, and the rotations of equipment – all of which saves money. According to SupplyChain 24/7, battery monitoring and regular scheduled maintenance can help a business avoid major pain-points caused by unexpected equipment issues and it can reduce the costs of doing business.
Value-driven reasons to invest battery monitoring technology
- Reduce frequency of battery replacement purchases. Replacement costs for batteries can be thousands of dollars, so prolonging battery lifespan can reduce what your business spends each year on battery units. With monitoring technology you can eliminate a common error – premature charging – which eats away at battery lifespans. Each charge costs a battery a cycle, cutting its lifespan. Knowing when to charge is as important as knowing how to charge.
- Reduce downtime and productivity losses.
Battery monitoring facilitates optimal fleet performance by eliminate habits that cut into warehouse productivity –like time lost from opportunity charging or swapping equipment mid-shift. For example, it provides accurate details – like when charges are occurring, targeted temperature readings, and the state of each charge – in real-time. - Management and right-sizing of equipment.
Detailed data analysis can help you determine, for instance, which trucks are causing amperage overloads and what operators are topping off. Monitoring can also help determine how many batteries. Three batteries for each forklift is typical, inventory today can possibly be reduced by “pooling and more effectively managing batteries”- through monitoring technology.
Battery monitoring delivers measurable ROI
When a manager can make educated adjustments – driven by real-time data on SOC, amperage, temperature, voltage, and recharge protocol – it leads to longer battery life and greater efficiency. Those small, important details determine what is working well, what is not, and deliver help ROI.
- For example, discharged batteries are left sitting and are not recharged right away. Batteries left sitting uncharged for extended periods allow for hard sulfation and significant loss of run-time strength, and it reduces the battery lifespan. Identifying this detail –and addressing it – can saves time, frustration and money.
- Battery watering is a typical maintenance requirement, but how it is done is rarely optimal and can be damaging to equipment and productivity. It is possible to over-water or under-water a battery unless a system is in place to monitor correct procedure.
With proper charging, cleaning and care, batteries have an expected lifespan of approximately 1,500 cycles — lasting approximately five years. But this only occurs under the right conditions. Battery monitoring technology provides the data needed to get the most life out of each unit and to provide optimum battery care.
Topics: fleet monitoring, telematic diagnostics, battery monitoring, value driven strategies, waste stream reduction, cost reduction