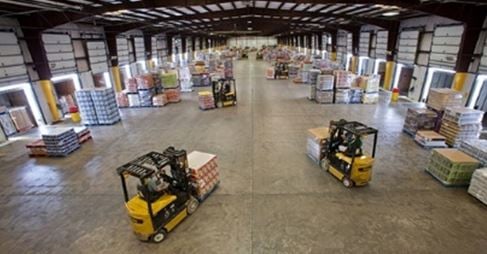
Tips for increasing warehouse productivity
Mobile weighing key to improving efficiencies to meet new consumer buying trends
Improving efficiencies in the warehouse is critical to meet current consumer trends, which are being driven by e-commerce and home delivery of groceries, to name a few. Warehouse productivity is affected by the type, size, and variety of materials being moved in the warehouse to meet these demands. While changes to these factors over time may increase or decrease performance, the one absolute affecting productivity is optimizing routine processes. Using mobile weighing technologies to reduce truck time at the dock (turn-over) can have one of the greatest effects on a company’s key performance indicators (KPIs).
Improving warehouse efficiencies critical for e-commerce and expansion of home delivery
According to a report on industrial trends developed by JLL, a professional services firm that specializes in real estate and investment management, e-commerce and its related logistics companies are looking to accelerate their investment in “last-mile” warehouse spaces in a bid to narrow the gap with brick and mortar stores. Global and domestic tenants are expanding their presence beyond a single mega-warehouse facility to multiple U.S. nodes, using logistics space to extend their reach to connect with customers. The logistics, distribution and third-party logistics (3PL) sectors that serve many retailers and e-commerce companies represented 24 percent of total leasing activity in the first quarter of 2017. [1]
“Online shopping and consumer demand for rapid delivery is changing what, where and how many distribution centers are needed to feed the consumer e-commerce beast. E-commerce continues to be the fastest-growing sector. In the third quarter alone, nearly 25 percent of total U.S. leasing demand came from e-commerce companies expanding their existing market footprints.” [2]
To meet the demand resulting from these trends, operators must step up to the plate and develop ways to improve warehouse efficiency and productivity.
Varied processes show the importance of warehouse productivity
Several routine processes affect warehouse productivity. These include order picking, trailer and truck loading, and receiving verification.
Order picking and packing – Order picking and packing is frequently the most expensive and complicated warehouse process. Timing and accuracy play a key role in successfully filling an order. These factors have a direct effect on picking labor costs and orders picked per hour metrics. Reducing time to complete a process/order is directly tied to customer satisfaction.
Trailer/truck loading – Getting a trailer loaded quickly and correctly improves cycle times and door turn-over. Quicker loading increases the quantity of units processed and reduces costs associated with wait times and reloads.
Receiving verification – Verifying weight and recording each load when it is received reduces receiving errors and provides a way of immediately addressing any errors. In addition, knowledge of incoming materials provides transparency for proper inventories and stock levels so orders are filled quickly and accurately.
Scale products increase productivity for warehouse applications
Scale products play a huge role in increasing productivity. For example, mobile forklift scales increase the on-time delivery percentage and number of orders per hour, while counting scales improve order accuracy percentage and increase the lines picked. Pallet jack scales reduce the cost per order. All in all, the right scale products help operators achieve overall equipment efficiencies. They will result in a reduction of overtime hours and cost-per-unit (CPU), and improvements in the units-per-hour (UPH). Labor utilization in general can be greatly improved.
Top tips for increasing warehouse productivity
Purchase equipment that can be utilized in multiple areas
By purchasing equipment that can be used in a variety of areas with a variety of processes, the cost of doing business will be reduced.
Reduce unnecessary motion/travel
Reducing cycle times and turns happens only after driving out inefficiencies. Equipment that allows operators to collect information quickly without unnecessary motion or travel will improve the process.
Drive out human error with technology
Look for methods and equipment that reduce human interpretation. Scanning of barcodes, sharing information over the network, and combining information from several processes are ways to improve.
Improve staff training
Technology can improve any organization if the people are properly trained to the process and operate the equipment. Train, train, and train again, to get the best return on one of your biggest investments – people.
Ensure good communication
Communication is critical in human interaction. It is also vitally important in processing information within the warehouse environment. Equipment that shares mission critical data through Bluetooth or Wi-Fi quickly shares information with billing and tracking systems and will improve warehouse operations.
Keep an eye on new procedures or technologies
Always look to implement new procedures and look to modern technologies – or different ways of applying old ones – to save both time and effort in daily warehouse operations. Focusing on continued improvement will improve the overall performance and lower the overall labor cost.
Measure performance
Make sure operations capture and manage critical KPIs. Understand and track critical productivity and costs on shipped orders, cost per box, and cost per line shipped. It is essential to measure and understand baseline information to be able to assess and put in place cost reduction measures. In short, you cannot improve if you do not measure!
Metrics illustrating relationship between warehouse productivity and profit
There is a clear relationship between warehouse productivity and profit. A medium size company with 40,000 pallet movements a year, in which 12,400 pallet movements require weighing, can save 3 minutes per weighment using a mobile fork scale compared to moving the load to a typical floor scale location. This saves the company approximately 37,200 minutes, or 620 man-hours. At an average warehouse rate of $35 per hour, the company could achieve a yearly cost savings of $21,700 ($1,808 per month). If one considers the cost of a mobile fork scale (including maintenance costs) the profitability gain would be more than $13,000 per year.
Fairbanks customers have realized a time savings per weighment utilizing the Fairbanks BlueLine WF Series fork scale on their forklifts. The weigh forks are completely wireless and use a rechargeable battery pack that works independently of the forklift. This savings was based on the time it took to drive a load to their floor scale and back to the trailer to be loaded compared to weighing immediately at the staging location. Trailers that previously took 3 hours or more to load were loaded in just over 1.5 hours. This substantial improvement in trailer loading times also reduced traffic back and forth from the scale, which in turn reduced dock congestion.
Look to mobile weighing devices to improve efficiency
Incorporating a weighing device into forklifts is an excellent way to reduce excess travel time to and from a traditional floor scale, thus allowing tasks to be completed more quickly.
References
[1] JLL, Industrial market starts 2017 on a positive note, 2017, http://www.us.jll.com/united-
[2] JLL, Industrial real estate expected to soar in 2018, 20 December, 2017
http://www.us.jll.com/united-