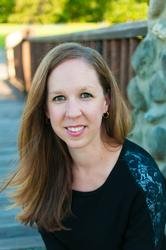
The Industry takes Safety seriously
In the 1960s, some 14,000 U.S. workers were dying on the job every year. A drumbeat was growing among the public to do something about the growing injury and fatality rates on the job, according to the Occupational Safety and Health Administration (OSHA).
Speaking in Congress during that decade, Rep. William A. Steiger told of the more than 400,000 Americans killed in workplace accidents and disease in the previous 25 years. “Not only has this resulted in incalculable pain and suffering for workers and their families, but such injuries have cost billions of dollars in lost wages and production,” he said, in an account on the OSHA website.
The push by the public and some government leaders resulted in the bill, The Occupational Safety and Health Act of 1970, which in turn led to the creation of OSHA, according to the administration.
In the years since, efforts to promote safe working conditions have continued. And in the material handling industry, business leaders and workers look for new ways to promote safe working environments.
How much progress is being made? What remains to be done? As the technological revolution changes much about daily life, it is also opening doors to the creation of products that make material handling workplaces safer.
This month, Material Handling Wholesaler asked those in the industry about the latest safety efforts and products.
Here is a look at some of the latest developments:
Forklifts
OE Attachments is launching a Forklift Safety Device featuring real-time residual load capacity, the company reported. The business, an Arrow Acquisition LLC company, is a manufacturing and distribution firm located in Lenexa, Kansas. It sells exclusively to OEMs, and specializes in the design and production of premium-grade forklift forks and attachments including skid-steers, telehandlers, excavators, backhoes, and tractor loaders.
“Our industry is long overdue for a product like this,” said Terry Melvin, CEO of OE Attachments, in a company press release explaining the new device. The business noted OSHA statistics naming forklifts as responsible for one out of every six workplace accidents. Within those figures, human error causes 70 percent of the accidents. Of fatal accidents, 67 percent are due to vehicle tipping, according to OE Attachments.
“You can’t look at those stats and ignore them, especially when you know you have the resources to be part of the solution,” Melvin said. The Forklift Safety Device is the result of several years of research and development. It uses a patented series of sensors and cameras providing real-time monitoring and residual load capacity via a touchscreen monitor installed inside the forklift cab, the company release said.
The device also gives auditory and visual alerts at all mast heights and positions whenever a safety hazard is imminent, the company said. It offers monitoring and response to external dynamic factors including acceleration speed, ground slope, mast tilt, load center, and more.
In short, the company says the device removes guesswork from operations. OE Attachments debuted the new device at this year’s ProMat in Chicago. Ahead of the debut, Brandon Tietz said the company was anticipating a flood of requests for information about the product. “This is actually something that is way overdue,” said Tietz, marketing and communications content strategist for Arrow Acquisition, in a phone interview with Material Handling Wholesaler. He said interested parties had already been contacting the company about the product, which had been tested with a handful of companies ahead of the roll out.
Related to forklift speed, Safety Systems & Controls recently unveiled nomad, a battery powered RF transmitter, to its Pace-One Zone Speed Control product line. The nomad creates a temporary mobile reduced speed zone for forklifts and other mobile equipment, according to the company.
“If there is an accident, a spill, a slick spot on the floor, inventory being counted, someone up in an aerial platform, if there is anything going on in an area where people or other equipment usually are not, nomad broadcasts a signal that automatically reduces all travel speeds around the area of interest on all Pace-One ZSC equipped vehicles thus creating a safer work space,” the company said, in an email to Material Handling Wholesaler.
Static electricity builds up in non-marking forklift tires can also cause risks. During a full shift of high-speed travel and heavy loads, forklifts can store static charges up to 50,000 volts, a major safety hazard, according to Camso. “Indeed, static electricity generated with non-marking tires is stored rather than dissipated, making shocks, sparks, power outages and facility damages ever-present hazards,” a statement from the company said.
Earlier this year, the company unveiled a non-marking anti-static technology (NMAS), a device that takes the form of “a telltale black dot on the face of the tread that allows static electricity to dissipate,” a release from the company said.
The device is made of “highly conductive black rubber” and is connected from the steel band to the tread face, acting as a plug and dissipating accumulated electricity on every rotation, the company statement said.
Gates and lifts
In the area of safety gates, the company Mezzanine Safeti-Gates, Inc. recently launched new methods for safety gate power operation, as well as sensors and technologies that can be used for the gates to communicate with fork trucks and AGVs, according to the company, which designs and manufacturers safety gates for elevated work platforms in distributions centers, warehouses and manufacturing facilities.
“We can also integrate our safety gates with technologies to report back into the overall supply chain software to understand what areas have been recently stocked or may be ready to be reloaded,” a release from the company statement said. In recent months, Mezzanine Safeti-Gates launched two new standards safety gates for loading docks that can be configured in a number of ways.
Meanwhile, Custom Equipment LLC, recently introduced the new PA-1030 push-around lift as “a safer and more productive alternative to ladders and scaffolding,” according to the business.
The lift allows users to manually maneuver into place and hydraulically raise and lower to the desired height. It is part of the company’s Hy-Brid Lifts next generation of lifts – the Push-Around Series, Pro Series and Zero-Turn Series.
“Contractors use these lifts every day, so we don’t waste any opportunity to include features that make their workdays better,” said Terry Dolan, Hy-Brid Lifts president & CEO, in a press release. “The PA-1030 includes convenience- and safety-boosting features sure to improve productivity and ease of use.”
The company reported that the push-around lift segment is “quickly becoming one of the fastest growing segments of lifts as maintenance and safety managers look for more effective ways to provide increased safety and productivity in applications where ladders and scaffolding are commonly used.”
Racks
Regarding racks, the experts at Worldwide Material Handling noted that repairs are less time consuming and frequently less costly than frame replacement.
The business, which helps customers identify danger signs of pallet rack damage and at-risk conditions in warehouses, noted that repairing warehouse pallet rack damage is not only cost-effective but efficient and offers a high return on investment. It also protects assets and reduces liabilities, said Courtney Zwintscher, marketing manager, in an email to Material Handling Wholesaler.
The business pointed out its Worldstop and WorldRev products as helpful in maintaining rack safety. The former offers a flue space divider that provides a fixed 6” or more flue space for industrial pallet rack applications. “The WorldStop is a patented product that replaces the need for backstop beams or netting, which can be more costly and less effective,” Zwintscher wrote.
And the WorldRev provides rack repair solutions for all types of pallet rack damage and offers nationwide installation services, she said.
Industrywide
At Helmar Inc., the company’s pedestrian lights are designed to prevent accidents by projecting a visible beam along the perimeter of the forklift to alert pedestrians of nearby forklift movement. The performance technology parts business describes the lights as weather, freeze and heat-proof, including a universal mount and UV-resistant poly-carbonate lens coming in a choice of red or blue. The lights provide an indication of a safe barrier for workhouse workers. Helmar has been selling the lights for four years and have been “a big mover” for the company, according to Paul Paciello, company president.
In a recent phone interview, he said the lights were initially sold for lift trucks and have moved into a variety of industrial equipment, like back hoes and earth moving equipment. “It is now becoming standard on new vehicles. It’s a very easy installation,” Paciello said.
In businesses working in kiln inspection and maintenance, Bricking Solutions has introduced Safety Inspection Cages and Personal Protection Tunnels to help create safe working conditions.
The former provides a sheltered area to repair and inspect the kiln, away from any falling debris, according to a company release. The tunnels provide safe passage in and out of the kiln. Both products are made to hold up to tough onsite challenges in an efficient manner, offering quick assembly and breakdown.“Kiln maintenance is a difficult task, even without the added safety concerns from falling debris,” said Lars Lindgren, Bricking Solutions president, in the release. “Our new universal safety cages provide protection customers can count on, sheltering them from debris as large as 250 pounds dropped from as high as 7 feet above the cage.”
Safety on the road
And how to ensure safety when hauling to a new location?
Troy Geisel, vice president of sales and marketing for Talbert Manufacturing, wrote a recent article regarding ensuring safety with heavy-haul trailers. Talbert bills itself as a manufacturer of “world class heavy haul and specialized trailers.
“The first safety consideration should be choosing a trailer that’s built for an operation’s specific load requirements,” he wrote, noting that making the right selection of trailer for load “eliminates the risk of structural failure as well as associated accidents and injuries.”
Geisel recommends calculating load capacity, state laws and regulations, including bride laws and kingpin-to-axle distance guidelines, load concentration and a trailer’s safety rating. “It’s important to take trailer capacity seriously. Each time it’s overloaded, the dynamics of the steel changes, much like a rubber band.
Eventually, the steel, and therefore the trailer, will break, increasing the risk for cargo damage, accidents and injuries,” Geisel wrote. “Purchasing the right trailer can be complicated but many manufacturers know capacity from top to bottom and can help contractors select the best trailer for their application.”
After matching trailer to load, Geisel recommends a pre-trip inspection. Look for damage or cracks in the unit frame, along with any other visible damage. “Inspect tie down equipment, such as chains, binders and straps, for broken parts and pieces and make sure they are rated appropriately,” he said. “Also ensure the trailer isn’t leaning or sagging to one side.” Geisel also advises checking brakes and tire inflation. Once on the road, he recommends considering the speed rating of a trailer.
‘Everybody can unify’ around safety promotion
This year, OSHA will hold its Safe+Sound week from Aug. 12 to 18 to celebrate the successes of businesses that have implemented safety and health programs in the workplace, according to the association’s website.
Businesses can either select activities to do at the workplace that week, or host an event for workers and / or the public. Once completed, participating businesses can download a certificate or web badge from OSHA. Some businesses are reaching out via an array of platforms to bring the safety discussion to the fore.
The Protective Guarding Manufacturers Association (ProGMA) has produced a series of educational videos on protective guarding equipment, which are shared via the association’s blog and are also viewable at mhi.org/progma/videos.
And this month, the Industrial Truck Association will present its sixth annual National Forklift Day, gathering together industry leaders and representatives to focus on safety. Held June 11 at the National Press Club in Washington D.C., the event helps create awareness for the need for continued operator training, according to Brian Feehan, Industrial Truck Association President, in a phone interview ahead of the event.
“It’s an initiative we’ve been working on a number of years,” he said, adding that in addition to spotlighting the need for training, the event stresses the importance of continually promoting safe conditions. The association has overseen the growth of the event in the past years, building out the program and its reach.
While pleased at this growth, Feehan said he believes there is always improvement that can be made. But he said the level of engagement does speak to recognition throughout the industry of the importance of promoting safety.
“It’s a testament to the overall industry,” said Feehan, who said even the fiercest of competitors can share a focus on safe working conditions. “Everybody can unify behind that message,” he said.
Eileen Mozinski Schmidt is a freelance writer and journalist based in the Greater Milwaukee area. She has written for print and online publications for the past 13 years. Email editorial@mhwmag.com or visit eileenmozinskischmidt.wordpress.com to contact Eileen.