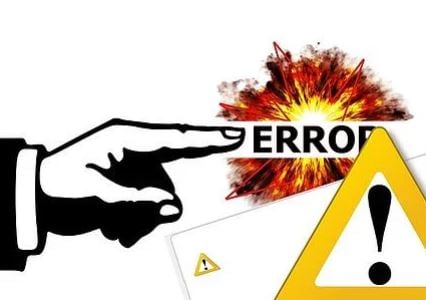
How to prevent Human Error in your Warehouse
Accidents will happen in a warehouse or distribution center, and human error is statically a major cause. Failing to identify the potential reasons for errors, ignoring on-the-job complacency, and disregarding poor driver habits or behavior will eventually cost you.
As with any workplace, your employees need to have best practices continuously reinforced. In a warehouse, repetitive tasks, long shifts, and a comfort level that comes with years on the job can cause drivers to become complacent about best practices.
But, preventing human error in your warehouse is possible. Identifying the biggest risks and acting to address them quickly can potentially avoid human error that can cost a warehouse operation in inventory, productivity, injuries, damages, and even human life.
Costly facts:
- The financial cost of just one forklift impact is about $38,000, plus another $150,000 in indirect costs. Those costs include damages to equipment, property, inventory, workmen’s compensation, and equipment down-time for repairs.
- A total of 882 fatal occupational injuries occurred in the warehousing and transportation industries in 2017 — that’s second only to the construction industry in terms of job-related deaths.
Prevent human error by identifying its potential
Potential is a funny thing. It can be a sign of future success or a warning about future errors. How can a manager recognize when an employee is showing potential for error? Begin with these five things.
- Worker behavior
Driver negligence or complacency can be addressed before an accident occurs. Use telematics to implement operation-specific safety checklists, which each driver must successfully complete before the equipment will operate. While vehicles are in use, telematics can monitor speed limits and control access to specific areas of the warehouse.
- Poor choices or increased speed
While vehicles are in use, telematics can monitor speed limits and control access to specific areas of the warehouse — for example, refusing entrance to areas designated for pedestrian traffic. All issues will be recorded in the operator report card.
- The root cause of previous accidents and injuries
Use historical telematic data to identify the underlying cause of previous impacts and who was driving or involved. Maybe it’s because of lack of training, risky operator behavior, or accident-prone areas of the warehouse, but easy-to-understand, real-time reports allow managers to make proactive changes to reduce errors from reoccurring.
- Lack of training, retraining or certification
Your software platform should track each driver’s certifications and training and identify when qualifications are about to expire. Operator report cards can also evaluate drivers on a regular basis to determine skill deficits. Ensuring that operators are certified and well trained helps to avoid human error, injuries, OSHA violations, and all of the associated costs.
The most effective way to reduce human error in your operation is to implement an advanced telematics system that warns about potential errors before they happen. It supports a proactive approach in preventing mistakes before they occur.
Topics: fleet drivers, injuries, operator training, human error, safety improvements, safety training, root cause,limit risks