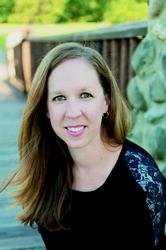
Boosting efficiencies in the warehouse in a tough labor market
Ken Ramoutar sees productivity as a multi-dimensional concept. Ramoutar, chief marketing officer at Lucas Systems, said when he started in the industry over two decades ago, few would have anticipated the coming labor force challenges.
“I’m not sure warehouse workers were viewed as a huge value and asset, and now they are,” said Ramoutar, who said the pandemic has accelerated this view. Now, the focus is on how to compete for the workforce, he said. “It’s more than productivity,” said Ramoutar, who said the traditional concept of more work for lower expenses has expanded.
“There’s a whole notion of what can I do, not to make everybody work faster, but how do I make the jobs easier. If I make the job easier, I am more likely to have a workforce that wants to be here and stay here,” he said, adding that this calculation includes labor competition from other warehouses.
Lucas Systems offers warehouse optimization solutions using AI, smart software and voice, according to the business website. The company’s tools are in over 400 warehouses worldwide, Ramoutar said. “We talk to customers all day long. The number one issue is the workforce,” he said.
Working smarter
Lucas Systems’ Jennifer™ software is the heart of the company’s software system, according to Ramoutar. “It’s the Alexus or Siri of the Lucas Systems,” he said, adding that the AI-based system incorporates a real voice and is somewhat like a hand-free system for a personal phone. “A distribution center is a busy place. Instead of looking down at screens or paper, workers can do their work and feel liberated,” Ramoutar said.
He said the system helps avoid errors and bolsters efficiency. “There are a couple of things Jennifer does really well. One is around travel pass optimization,” said Ramoutar, who said the system is constantly computing the most efficient travel path inside the warehouse to get the work done, sometimes coordinating pathways for 100 to 200 workers at a time.
Ramoutar said running smarter instead of faster using a system like Jennifer can help boost productivity in the range of 20 to 40 percent. Lucas Systems tends to work with mid-size to larger companies, and the sizes of warehouses are increasing, Ramoutar said. “The warehouses are getting bigger. And everybody loves e-commerce. Where’s that all going? That’s accelerating,” he said.
Meanwhile, the labor needs are not going away. “All of the data around the labor issue suggest it’s not going to get better,” said Ramoutar, noting that the retiring Boomer generation is 4 million greater than Generation Z. Added to those numbers is the need to appear to younger workers.
“Tech plays a pretty big role,” said Ramoutar, who said handing a new employee a clipboard and sending them into the warehouse is not going to appeal to many younger workers. “Companies are going to have to get better at attracting and keeping the labor,” he said. Software and tools like those provided by Lucas help check multiple boxes of need, Ramoutar said.
“Software is the fastest thing you can do to get returns,” he said. “As soon as you start running, you’ll get returns right away.” Jennifer was designed to be user-friendly, and Ramoutar said workers typically find that after a few hours that they are comfortable with the technology.
The system includes automatic speech recognition and includes over 30 language options. “This is a big deal for some operators. They may have a fairly multicultural workforce. With Jennifer, they can speak their native language and still work in the warehouse,” said Ramoutar, adding that this is appealing for workers. “It’s also attractive for the workforce. We’re going to give you stuff easy for you to use,” he said.
The next wave of worker engagement will be using more video game mechanics in the tools, Ramoutar said. “There’s a lot of things that have come out of the gaming industry that can be applied in a service environment,” he said, naming features like competing against oneself or other workers, getting feedback and earning incentives. “It’s kind of making work fun. We think there’s a big opportunity for that,” he said.
It all adds up to making the warehouse more dynamic, especially as warehouses handle ever-larger volumes of orders, according to Ramoutar, who said Lucas Systems’ will continually recalculate while operating. “We are constantly making sure everything is optimized,” he said.
Productivity at the end of the line
At SupplyOne, productivity is also a key area of focus. The company, a distributor of end-of-line packaging equipment, operates in both manufacturing and distribution centers.
Chip Reavley, senior vice president of packaging automation, handles oversight and responsibility for the packing equipment and automation team, which includes equipment engineers and factory certified technicians. End-of-line packaging can also be referred to as secondary packaging, according to Reavley.
“They’re really synonymous,” he said, noting the wide array of automation points covered by secondary packaging. The company bills itself as the largest independent supplier of custom corrugated and other value-added packaging products, equipment, and services in the U.S.
SupplyOne offers a full gamut of automatic and semi-automatic case erecting and case sealing systems, strappers, banders, palletizing and wrapping equipment, as well as associated consumable including custom or stock corrugated films, tapes, strapping, and other materials, according to a SupplyOne press release.
The company provides mid-sized manufacturers, food processors, and medical and e-commerce companies “leading packaging programs and complete packaging solutions,” the statement said. SupplyOne’s approach is to offer best-in-class solutions to customers, according to Reavley.
“It allows SupplyOne to offer state-of-the-art proven solutions,” he said. The pressure of the labor market continues to influence industry developments, Reavley said. “The labor market has, and continues to be, challenging,” he said, referencing both finding and retaining skilled workers.
While labor eliminations were originally a concern with automation, Reavley said the current trend for many is to implement automation to allow for labor reallocation. “It’s so hard to find good labor. They’re redeploying into other areas and automating,” he said.
The interest in automation, overall, has been on the rise, according to Reavley. For those unsure about pricing on solutions, he will sometimes ask customers if they would take the end-of-line automated solution if it were free. When they respond in the affirmative, it helps focus on why the solution would work well, according to Reavley.
In one case study, a manufacturer realized a 30 percent increase in productivity following the incorporation of a SupplyOne secondary packaging solution. “The productivity boost really began immediately,” said Reavley, who said the complete solution incorporated by the company was a coordinated effort between the SupplyOne team and the operation.
SupplyOne offers both standard off-the-shelf automation and customized products, according to Reavley, who noted that the company offers careful attention to detail with every project.
SupplyOne’s statement said the company is committed to uncovering hidden costs within customers’ packaging expenses. This focus can lead to cost savings in any number of areas, Reavley said.
“They might be using a 3-inch-wide tape when packing to cover the box more and we’ll go in and realize they can go to a 2-inch tape,” he said, adding that this type of adjustment can lead to significant cost savings. Or the team from SupplyOne can help achieve efficiencies in real time, like switching a left-handed worker and right-handed worker to different work spaces to increase productivity.
Product benefits
The types of supplies used within the warehouse can also provide ongoing efficiencies, according to ORBIS Corporation. The company is a provider of reusable plastic containers, pallets, dunnage, and bulk systems that improve the flow of product all along the supply chain, according to the business.
James Riegleman, product manager at ORBIS, works with distributors to supply pallets for retail, food manufacturers and pharmaceuticals. He said reusable and plastic packaging allow for a more efficient and effective process. “You get that extended service life and reliable repeatability from plastic,” said Riegleman, noting the example of the company’s new ORBIS Odyssey HD Open Deck Pallet.
The 40×48 size pallet was tested in a third-party validation process at Virginia Tech and reached 400 cycles of use before the test concluded. A wood pallet, by comparison, lasted 11 cycles, Riegleman said. The Odyssey was designed primarily for food manufacturing, according to Riegleman, and corresponds with the increased use of automation.
Automation is effective when running smoothly, which Riegleman said is difficult to achieve when associated products cannot be relied upon. “We work with automation integrators from the start,” he said, adding that design focus at ORBIS is about everything in the warehouse working together. While ORBIS offers standardized products, the company can customize them when needed.
“The great part of being the manufacturer is if we don’t have the solution, we can make it,” Riegleman said. In addition to automation, another big focus for warehouse operations is sustainability, according to Riegleman. He said ORBIS offers a recycling program in which the company buys back the used products from customers and turns them into additional future products.
In addition, Riegleman said the company’s focus is on efficiency. ORBIS provides a full gamut of asset management options, like cleaning, inspecting and data for tracking. The company’s reusable packaging management, or RPM, is helpful for several of the businesses’ large consumers, Riegleman said.
About the Columnist:
Eileen Mozinski Schmidt is a writer and journalist based in the Greater Milwaukee area. Email [email protected]. If your company would like to be featured, email [email protected]