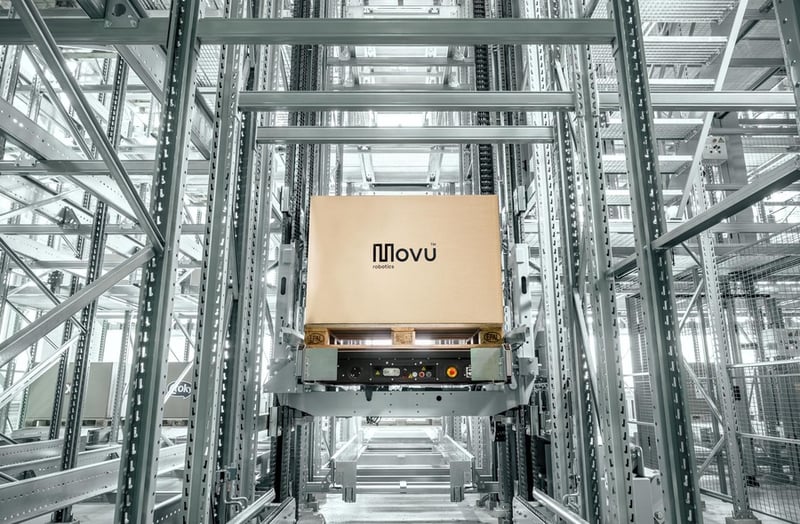
Shuttles or stackers?
When considering automated warehousing, stacker cranes have often been the default storage and retrieval choice for pallets and bins. Shuttles, however, are increasingly being seen as the more efficient, flexible, and sustainable alternative, as Stefan Pieters, CEO of Movu Robotics, explains.
Most firms that must move quantities of palletized goods moving in, out or through a warehouse are familiar with that old stalwart – the stacker crane. Indeed, it is no exaggeration to say that in many cases the warehouse is designed and built around the craneage.
That, though, is far from ideal, whether viewed in terms of operational efficiency or through the increasingly important prism of sustainability.
Stacker cranes are undeniably chunky. They consume a lot of material in their construction, and a lot of energy moving all that mass around. Partly as a result they require significant upfront capital investment, which is a particular challenge for smaller businesses with budget constraints.
They are also very wasteful of available, expensive, floor area. They require generous aisle space to work in which reduces the overall storage density within the warehouse. They are not well suited to more space-efficient deep storage. They require the site to be all on one level, which for a warehouse of any magnitude often means building on a flood plain. They may demand floors to have a greater load-bearing capacity and place other demands on the building’s structure and services that are difficult to meet in older facilities. Also, a stacker crane layout cannot make effective use of the irregularly shaped pockets of the site that are common in older developments or in urban areas. On some warehousing sites well over 50% of potential storage space is reckoned to be wasted.
Being complex systems, stacker cranes are demanding of meticulous planned maintenance, which must be carried out in situ, and whilst that is in progress that aisle is essentially out of action. Similarly, any breakdown or malfunction will disrupt operations – they constitute a ‘single point of failure’ – just one apparently minor problem can render an entire aisle’s inventory inaccessible.
Perhaps most fundamentally, warehouse systems built around a stacker crane concept are fundamentally inflexible. The specific configuration of locations, aisles and cranes places a fixed limit on the maximum throughput of the facility: increasing throughput is likely to require a fairly large scale and expensive redesign and rebuild.
Shuttles and space
Stacker cranes still have their place – particularly for heavy goods, and where maximizing the use of the vertical space is imperative, although as we will see that is less of a differentiator nowadays. But for many palletized warehouse operations there is an increasingly attractive and viable alternative in the form of shuttle systems, such as those manufactured by Movu in alliance with our group partner stow Racking.
Pallet shuttles are small vehicles with a low height, and with a footprint essentially that of the pallet they are moving. They move on rails within the storage lanes of the racking system to bring pallets to and from a loading/unloading end aisle which can also be used to transfer pallets between storage lanes. Shuttles operate in two dimensions in each ‘layer’ of the racking system but can be transferred vertically as well as between lanes. The latter is carried out automatically, through the management system and, unlike some earlier systems, without the use of a forklift truck to affect the transfer. Movu Atlas shuttles, for example, can carry pallets of 1 m x 1 m, or 1 m x 1.2 m, weighing up to 1,500 kg.
Besides greatly reducing the amount of ‘wasted’ aisle space required, this approach has several advantages. There is no particular limit to vertical height – 18 meters is commonplace, and we have one client whose racking extends to an eye-popping 46 meters. Odd-shaped pockets of the site, whether this is in the plans or because of uneven ground, can be brought into use economically simply by using some shorter lanes. And because shuttles, unlike stacker cranes, are in no sense fixed, it is relatively straightforward and economical to reconfigure the racking if needs be – the racking itself is of modular design.
Being battery-powered and mobile, shuttles can be moved out of the way of operations for battery charging, routine maintenance, or in the case of breakdown, so not impairing the operation of the warehouse. At times of peak activity, the number of shuttles in use can be increased – either across the warehouse or by transferring shuttles between lanes or levels, to meet increased demand in a particular section of the warehouse. Shuttle systems can thus be fully scalable and flexible.
Sustainability advantage
In terms of sustainability, as well as making better use of scarce real estate, shuttle systems employ much less material both in their construction and in terms of building modifications. And the saving in energy consumption simply from not having to move massive cranes around is substantial – a shuttle weighs 300 kilograms; a crane may weigh up to 15 tons, and so a shuttle system can be up to five times more energy efficient than craneage.
The shuttle concept can also be applied to transporting bins of material in goods-to-person picking operations. Carrying a lighter loading (up to 50 kg) enables a significant difference from pallet shuttles. Movu’s escala shuttles, for example, can work in full 3D, moving up and down ramps to access different storage layers – a bit like a multi-story car park.
Integrating with Autonomous Mobile Robots (AMRs), picking arm robots or with other forms of automation permits a high degree of automation that can yield further sustainability benefits. These can support areas of a warehouse that does not have to support regular human labor so can be run ‘lights out’ or with reduced heating. Cold store operations, meanwhile, can be made more energy efficient – Movu equipment, for example stands out as capable of working in temperatures down to -25° C.
Bringing easier automation to warehouses
Shuttles offer a flexible, scalable, modular approach to automation. Systems are quick to install, even in existing buildings and on awkward sites, simple to integrate, and easy to reconfigure or expand with minimal impact on ongoing operations. An operator can start small – shuttle systems can be viable for sites with as few as 5000 pallet locations – and expand as finances or business allows: we have users with as many as 80,000 pallet locations.
Consumer requirements, especially for e-commerce, combined with rising pressure on resources from land and labor to energy, mean that warehouse automation is imperative. But in these uncertain times, heavy upfront investment in solutions that are in their nature limited and inflexible may not be the best option, either now or on your business growth path. Modular shuttle systems, such as those provided by Movu Robotics, offer an economically and environmentally more sustainable alternative.
About the Author:
Movu Robotics, member of stow Group, is a new warehouse automation brand that stands out by bringing easier logistics automation solutions to the world’s warehouses. Employing more than 300 employees by end of 2023 across Europe and the US, Movu Robotics operates globally and expects order intake of more than €300 million in 2023. Movu Robotics offers a complete portfolio of automated technologies for efficient warehouses. This includes the pallet shuttle “Movu atlas” for multiple deep storage, the AMR solution “Movu ifollow” for collaborative picking or transport of pallets, the robotized 3D storage and fulfilment system “Movu escala” and the integrated picking robot arm “Movu eligo”. All Movu systems are controlled and managed via their own warehouse execution software. Movu Robotics’ headquarters in Lokeren, Belgium, combines a 5,000 square metre large office area with a 10,000 square metre surface for logistics and manufacturing operations under a single roof, next to a state-of-the-art experience center – one of the biggest in Europe – where the latest technologies are showcased live to customers and partners.