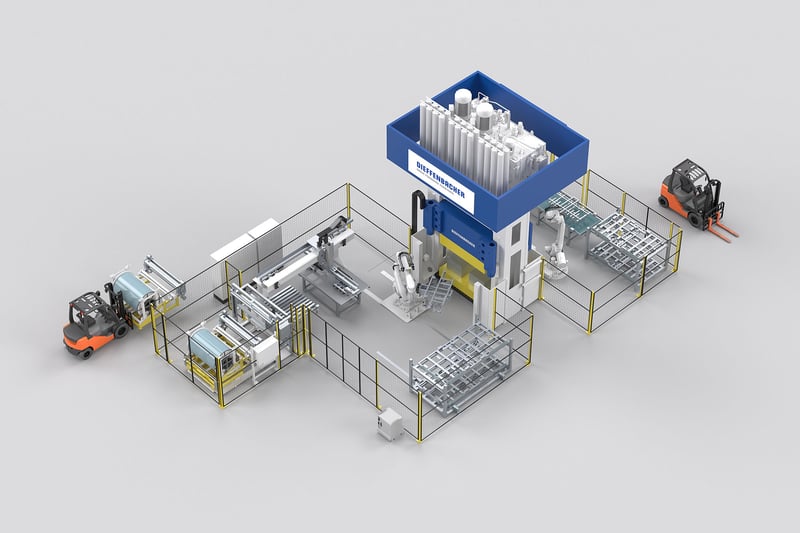
DIEFFENBACHER optimizes material utilization
Material-efficient carbon and SMC component production with Fiberforge and SMC cutting and packaging system.
More than anything else, sustainable production means saving resources and using valuable raw materials as efficiently as possible. With its Fiberforge tape laying system and the fully automatic SMC cutting and packaging system, DIEFFENBACHER, a supplier of complete composite systems, offers two solutions that significantly reduce material consumption in the production of carbon and SMC components.
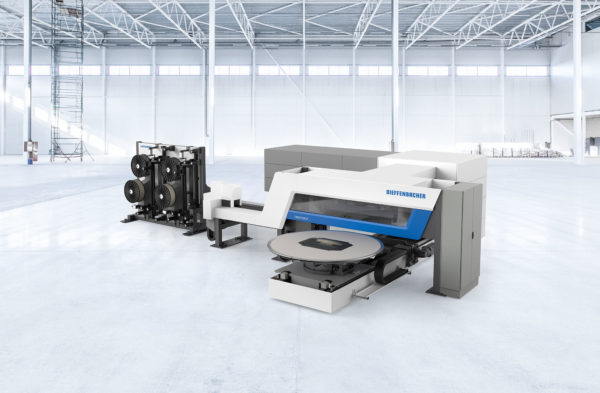
Interior of an empty warehouse
The DIEFFENBACHER Fiberforge enables the fully automated production of layups from thermoplastic UD tapes for small and large series production. Using the special DIEFFENBACHER nesting method, the tapes are cut to the required length and combined into a layup in a load-oriented manner via a rotary table. “In the process, the tape ends can be trimmed at any angle between -45° and 45° to produce a contour with minimum waste,” explains Marco Hahn, Sales Manager of the Forming Business Unit at DIEFFENBACHER.
Different tape types, even with varying widths, thicknesses, and reinforcing fibers, can be combined in one component without manual intervention. “The high degree of automation enables consistent component quality and high flexibility in component design. Compared to organo sheets, our customers achieve high material savings with the Fiberforge. In one sample application, we achieved just 6.7% waste with the Fiberforge, while with the organo sheet there was more than 50% waste. In addition, the angle cut enables diagonal cuts of the tapes and thus saves valuable material,” says Hahn.
By combining length and width cuts, the DIEFFENBACHER SMC cutting and packaging system can generate all conceivable cutting patterns. In accordance with the desired lay pattern, the intelligent nesting control determines the cutting pattern and optimizes material use. Weight deviations from the raw material are measured and actively compensated for in downstream stacking. Error-prone manual steps that could affect production quality are eliminated. “Combined with our lay-up robotics and our stacking gantry, which is used to package individual blanks before they are inserted into the die, we offer our customers maximum flexibility for realizing the most complex lay-up patterns,” states Hahn.
“We also help customers produce more sustainably, efficiently, and cost-effectively with our solutions for minimizing energy consumption, which includes our short-stroke presses and adaptive accumulator management,” Hahn adds. “Together with our customers, we are continuously working on implementing further ideas to increase sustainability.”