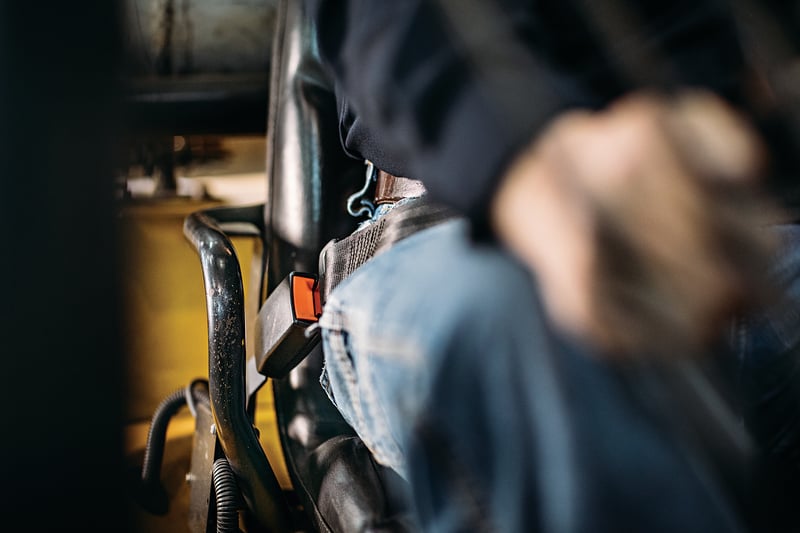
Essential safety reminders to protect your crews and your bottom line
Brush up on important safety reminders this Forklift Safety Day
Forklifts are key to workplace productivity but introduce a variety of hazards—many of which can be mitigated with an educated, proactive workforce. In fact, studies show that roughly 70 percent of all forklift-related accidents could have been avoided with proper training.
While Forklift Safety Day provides an opportunity to celebrate workplace safety each year, safety is something that should be top of mind for material handling professionals 24/7, 365 days a year. A simple way to keep crews informed and engaged is by conducting ongoing safety meetings. Here are a few important forklift safety tips to share with crews this June—and throughout the year.
Critical forklift safety reminders
- Complete a routine check of equipment before operating and notify management of damages or problems.
- Wear personal protective equipment as provided by the employer including hard hats, protective footwear, and high-visibility clothing.
- Always wear a seatbelt while operating a forklift. It’s important for operators to buckle up while operating a sit-down forklift, as overturned forklifts are a leading cause of forklift-related accidents. Wearing a seatbelt can save operators from being crushed by a machine’s overhead guard or roll cage in the event of an accident.
- Keep loads within the forklift’s weight capacity. By exceeding the weight capacity of a forklift, employees can greatly increase the risk of tipping the machine. These load capacities can be double-checked in the equipment’s operating manual and are also listed on the machine itself.
- Operate at a safe speed, use the horn when vision is obstructed, and use caution on grades or ramps. Operators should use the horn to alert pedestrians or other forklift operators nearby to avoid an unnecessary collision. Take corners and turns slowly to minimize the risk of tipping.
- Set the parking brake, lower the forks, and set any controls to neutral when finished operating. Safely parked machines reduce the risk of unintended movement when left unattended. If a forklift is parked on an incline, employees can further secure the machine with wheel blocks.
Different forklift fuels require different safety procedures. It’s important for crews to be aware of fuel-specific safety measures, depending on what they use on-site—this will not only help them get the most out of their equipment and workday but will help prevent potential injuries, too. With 90 percent of Class 4 and 5 forklifts across the United States being powered by propane, it’s important to share proper propane safety practices.
Best practices for handling propane cylinders
- Wear protective gloves.
- Keep open heat, flames, and ignition sources away from cylinders and refueling equipment at all times.
- Handle cylinders carefully, making sure not to drop, throw, or drag them.
- Use proper lifting techniques when lifting cylinders.
Safety measures before and after operating propane-powered equipment
- Inspect cylinders before operation. Check cylinders for rusting, dents, gouges, and leaks. Cylinders that show signs of wear or leaks shouldn’t be used and may need to be replaced, even if within the cylinder’s requalification date.
- Secure the pressure relief valve on the cylinder. Operators should check that the pressure relief valve fitting is roughly 180 degrees from the forklift’s locating pin.
- Close the service valves on cylinders when not in use. This helps prevent potential injury around internal combustion engines and unintended fuel loss.
- Store propane cylinders in a secure rack or cage. The cylinders should be stored horizontally with the pressure relief valves in the uppermost position, and operators should use proper lifting techniques when removing cylinders from storage and placing them onto a forklift.
- A propane cylinder storage rack should be located a safe distance from heat or ignition sources, away from stairwells and high traffic areas, and protected from exposure to the elements.
Fortunately for crews operating propane-powered forklifts, they can lean on their local propane supplier for support. Local suppliers can provide safety training opportunities, inspect cylinders each time they’re exchanged, remove damaged cylinders from service, and repair or replace leaky valves and O-rings on cylinders as needed. Additionally, depending on which refueling option businesses choose, propane suppliers can teach forklift operators how to refill cylinders themselves (on-site refueling) or can refill cylinders for them (cylinder exchange program).
Visit Propane.com/SafetyFirst to download PERC’s free safety toolkit or to learn more about propane forklift safety.
About the Author:
Matt McDonald is the director of off-road business development for the Propane Education & Research Council. He can be reached at matt.mcdonald@propane.com.