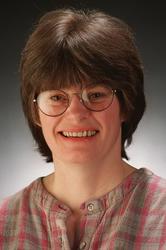
New technologies streamline warehouses
Probably before you see self-driving vehicles on the roads, you will see them in warehouses.
The OTTO self-driving vehicles (SDV) are ready for use in warehouses, said spokesman Meghan Hennessey. Designed by OTTO Motors, for material transport, they are already at work in factories. Although OTTO isn’t in any warehouses yet, it is ready and the company is working with a number of organizations to build out plans.
“One of the core advantages of the OTTO SDV is to improve productivity in the workplace. We’ve developed OTTO to have human-like characteristics – it can move dynamically through its environment, detect and avoid obstacles and indicate to its human colleagues where it’s going to move. The self-driving vehicle is a piece of the Industry 4.0 vision that strives for lights-out operation. As advanced technologies, including OTTO, move into the industry, it will take on the dull, mundane tasks that are, of recent times, difficult to fill by people, and people will begin to move into more complex roles, such as business strategy, sales or controls engineering,” Hennessey said.
She said that as with the horse and buggy to the car, or the computer to the accountant, self-driving vehicles will displace some people from the jobs that they are currently doing in order to create a more productive workforce. The roles people will fill will require creative thought, complexity and empathy.
“These roles will typically be of higher value, meaning those employees will experience better job satisfaction and maintain a higher quality of life. It won’t happen immediately, but rather be a gradual shift over time,” she said.
The OTTO 1500 is made for heavy-load material transport and is designed to move palatalized loads over long distances. Once integrating OTTO, return on investment is reached within 12 to 18 months, she said.
“The solution offers infrastructure-free navigation, which means it does not require the use of beacons, barcodes or pre-planned laser paths. Because no infrastructure is required, it allows for a very flexible system; minimal changes are required to integrate the system into a facility. OTTO uses the same underlying technology that is used in the Google driverless car, which is to say that it uses sensors as well as perception and navigation software,” Hennessey said.
It avoids obstacles and is collaborative, she said.
“It uses sounds and light patterns that are similar to cars we drive on outdoor roads. For example, when it turns right, the right turning signal blinks. These queues help warehouse staff understand its behavior and work closely with it. Also, because OTTO is a very flexible system, it can be programmed to the extent that it pics up a package on the right side of a right-handed person for the morning shift, and then changes to the left side for a left-handed person in the afternoon shift,” Hennessey said.
Other changes in the warehouse have already begun.
Starting Jan. 1, 2017, the California Energy Commission requires that all battery chargers sold in California must operate at certain levels of energy efficiency and that charging technologies manufactured on or after Jan. 1, without the CEC regulatory approval logo, cannot be sold or supplied in California.
“For consumer products, the Department of Energy’s similar (actually more stringent) requirements will apply in all 50 states in July 2018,” said Chris Botting, head of research engineering for Delta-Q Technologies. “CEC’s requirements for industrial chargers may spread piecemeal at the state level; Oregon has already adopted them, and others have considered adoption.”
But it is in effect a national standard. “That’s how we view it. No original equipment manufacturers will want to sell two different products in different states,” Botting said.
“Older ferroresonant and silicon controlled rectifier-based chargers will be practically eliminated from the market. This will also result in meaningful reductions in electricity usage for end users – which is good for the environment and the bottom line,” he said. ”Check that your battery charger is CEC listed; ask your charger supplier, or visit California’s online appliance efficiency database. If efficiency improvements need to be made, use a high-frequency switch-mode charger that uses power factor correction. Minimize AC and DC cable resistances by keeping lengths short and using heavier gauge wires. Select a higher nominal voltage (ex. 48V instead of 24V). Reduce parasitic AC and DC power draw, and don’t use indefinite float charging. If necessary, switch to a more energy efficient battery chemistry: from flooded lead acid, to sealed lead acid or to lithium ion,” Botting said.
The way forklifts work and interact with their operators is also changing.
“The forklift is becoming a mobile information technology hub capable of collecting and processing data from products, operators, the environment and other material handling systems,” said Andy Smith, director of marketing product management for Crown Equipment. “We will continue to see new technology being introduced that will create a fully connected forklift that provides visibility into operations in support of a business’ desire to simplify labor management, achieve greater cost control and strategically adjust to evolving needs. Forklifts not only move goods, but with sensors decreasing in cost, they can increasingly track and record data.
“The good news for those looking to scale their investment is that a connected forklift is not an all-or-nothing proposition. A minimal investment in a connected forklift can provide savings and benefits that can fund future investments that expand the scope and value of the program,” Smith said. “New technologies are disrupting warehouses globally at a faster pace than we’ve seen before.”
But with enhanced connection between operators and forklifts and managers with employees, the result can be a safer and more productive environment.
The environment must also be healthy and safe. “There is an increasing demand for more environmentally friendly, low emission options throughout the market and more automation and integration with existing systems. At the same time, the market is also emphasizing operator friendly features as the industry becomes increasingly aware of the importance of ergonomics,” said Justin Engel, marketing specialist for Starke Forklift. “And, as always, there is always a push towards maximizing storage density with narrower aisles and higher storage options. As far as the push towards sustainability, Stärke utilizes high efficiency AC motors in all of our electric forklifts and lift equipment, while also utilizing CARB IV engines for our LPG forklifts. We’ve also addressed the issue of operator comfort by reducing vibration and noise (particularly in our new XVI line of forklifts), improving visibility to reduce unnecessary/awkward movements, and ensuring the ergonomic design of our control systems.”
Scott Wiley, industrial product line manager for Akro-Mils, sees technology and security as trends to watch. Companies use technology to “do more with less,” he said, including managing inventory and controlling costs. Companies protect their investment by limiting tool use to those who need them and having safe storage. “Some of our new products that tie directly into these trends are placing keyless locks on storage cabinets and having lockable work carts and tables,” Wiley said.
Mary Glindinning is a freelance writer who has worked at daily and weekly newspapers for more than 20 years. She lives in rural Shullsburg, Wis. E-mail editorial@mhwmag.com to contact Mary.