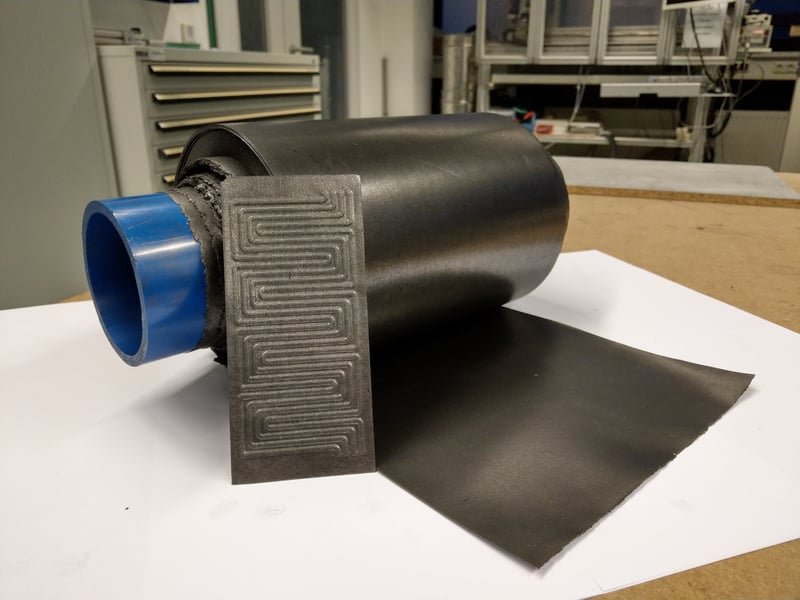
Flexible bipolar polymer plates open the way for compact batteries
Whether used in stationary energy supply or electric car applications, conventional battery systems involve several interconnected individual cells, which presents certain disadvantages in terms of efficiency and manufacturing. With bipolar batteries, on the other hand, the individual cells are plates which are arranged in compact form as a stack.
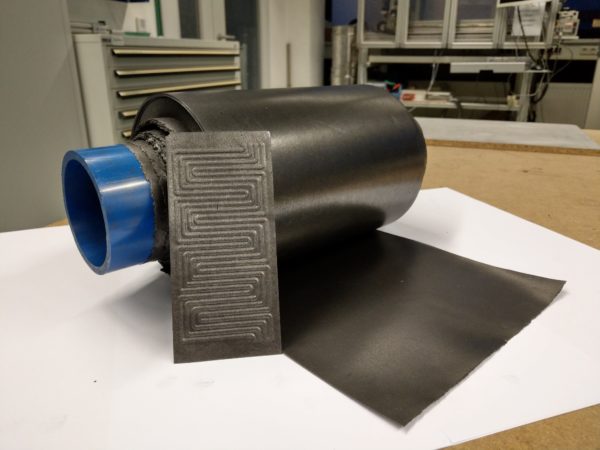
- The Fraunhofer Institute UMSICHT is currently developing a new type of bipolar plate which is flexible and extremely thin and which allows bipolar batteries to be cost-effectively manufactured.
- The Fraunhofer researchers will be presenting their innovation at Stand C22 in Hall 2 at this year’s HANNOVER MESSE, which runs from April 1 – 5.
Hannover/Oberhausen. Conventional battery systems are extremely complex. They usually consist of several individual cells that are connected with each other by wires. Not only is this structure costly and time-consuming to produce, it also entails the risk of hot spots – areas where the wires get too hot. In addition, every single one of these cells has to be packaged, meaning that a large portion of the battery consists of inactive material that does not contribute to battery performance. Bipolar batteries are designed to solve this problem by structuring the individual cells as flat plates and connecting them by stacking them on top each other. However, this presents its own challenges, because either the bipolar plates are made of metal and are thus prone to corrosion, or they are made of a carbon-polymer composite, in which case they have to be at least several millimeters thick, owing to certain manufacturing constraints.
Material savings of over 80 percent
A team of researchers at Germany’s Fraunhofer Institute for Environmental, Safety and Energy Technology ( Fraunhofer UMSICHT ) has now developed an alternative. “We manufacture bipolar plates from polymers that have been made electrically conductive,” says Dr. Anna Grevé, department head at Fraunhofer UMSICHT. “In this way, we can produce very thin plates and – compared with conventional cells connected by wires – use 80 percent less material.” The material offers numerous other advantages as well, such as the fact that it does not corrode. Another major advantage is that the material can be subsequently reshaped. This makes it possible, for example, to emboss structures, which is important for fuel cells. Moreover, the innovative new bipolar plates can be welded together, so the resulting battery system is totally gas and liquid-tight. Conventional bipolar plates, by contrast, are unsuitable for welding due to the thermal and mechanical stresses on the material during manufacture. Joining them in such a way that neither gases nor liquids can pass through the joints requires seals. However, seals quickly become porous, plus they take up space. A further advantage of the new material is that it allows the researchers to adapt the properties of the bipolar plates to specific requirements. “We can make plates that are so flexible that you can wrap them around your finger, as well as ones that are completely rigid,” explains Grevé.
Cost-effective roll-to-roll manufacturing process
The primary challenge consisted in developing the material and the manufacturing process. “We use commercially available polymers and graphites, of course, but the secret is in the recipe,” says Grevé. Because the material is made up of about 80 percent graphites and only about 20 percent polymers, the processing methods have little in common with ordinary polymer processing. The researchers opted for the roll-to-roll process, which allows cost-effective manufacturing, and applied their advanced technical expertise to adapt it to their requirements. The key was to ensure that the ingredients were distributed homogeneously in the resulting plates and that the plates were mechanically stable and completely gas and liquid-tight. Because of the initial structure of the materials, this was no easy challenge, but the experts at Fraunhofer UMSICHT were more than equal to it. “We were able to fulfill all requirements within the one process, meaning the plates are ready to be used straight out of the machine,” Grevé explains. Another advantage of the chosen process is that the plates can be manufactured in any size.
Presentation at HANNOVER MESSE
The researchers are already able to produce sample quantities of the new bipolar plates. Together with SAUERESSIG GmbH + Co. KG, they have taken the method used for producing bipolar plates for fuel cells and translated it into a continuous process for battery plates. The project was funded by the German Federal Ministry for Economic Affairs and Energy (BMWi). At HANNOVER MESSE (Hall 2, Stand C22), Grevé and her team will be showcasing a 3.2 square meter bipolar plate that enables the construction of large-scale redox flow batteries.