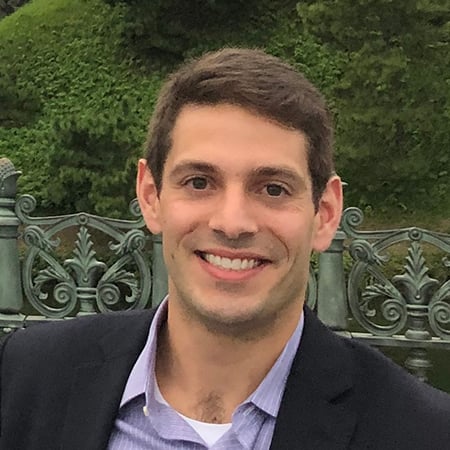
The Four Pillars of Warehouse Orchestration: Why you need more than just “Better”
Every warehouse is on a mission to improve, trying to be a little better every year. But let’s be honest—the warehousing landscape has changed so drastically that “being better” just doesn’t cut it anymore. With rising complexities, tighter margins, and growing customer demands, it’s no longer about tweaking what you already do. Now, you have to be different.
Warehouses today are more complex than ever. You’ve got robotic systems, human workers, fluctuating inventories, and rapid demand shifts—balancing these moving parts has become necessary to maximize throughput and ensure the operation doesn’t grind to a halt. Add to this the fact that warehousing is in the middle of a leadership shift—10 years ago, site leaders had 15 years of experience running a smooth operation. Today, they have less than four years on average. It’s no wonder things can feel like they’re spinning out of control.
Enter orchestration is about finding new ways to optimize your warehouse operations. Warehouse orchestration is no longer a luxury; it’s a necessity. It’s about ensuring everything flows smoothly. It can be summarized as advanced optimization that helps you manage a site by focusing on four critical pillars: Labor Planning, Inventory Flow Management, Human/Robotic Task Handoffs, and Space and Constraint Optimization.
Labor Planning: Putting the Right People in the Right Places
Labor planning is the backbone of any efficient warehouse. You can’t just throw workers at a problem and hope for the best—across all of the complex processes in a facility, you need to place people where they’re needed strategically. One minute, it’s all about bulk orders; the next, it’s a flood of e-commerce pick requests. Without the right labor plan, your team either stands around or scrambles to catch up.
Orchestration platforms keep you ahead of the curve. By planning out optimal workflows across multiple shifts and adjusting labor accordingly, these platforms ensure you have the right number of workers at the right time in the right areas. You’re not overstaffed when things slow down, and you’re not scrambling when the rush hits. The result? A warehouse that runs smoothly, where employees are productive, and throughput is maximized.
Inventory Flow Management: Keeping Goods on the Move
Efficient inventory flow is like having a highway system with no traffic jams. When inventory constantly moves to the right place at the right time, your operation runs like clockwork. But too often, warehouses resemble a parking lot at rush hour, with goods not being brought in on time to meet outbound demand, creating delays and forcing workers to waste time on unnecessary movements. This is extremely costly to warehouses, where even a .1-.2% increase in “controllable cuts” can result in $500K – $1M in lost business PER MONTH.
Orchestration changes the game by ensuring that inventory flows smoothly. It automatically prioritizes when items flow through the facility to ensure that throughput is delivered and trailers leave on. It even balances how the trade of shipping more product versus being late (for example, if you have an inbound arriving in an hour that has ten pallets that are needed on an outbound, it might make sense to delay the outbound for 1 hour to cross dock those ten and achieve a better fill rate).
Human/Robotic Task Handoffs: Maximizing Efficiency Through Collaboration
In a warehouse, humans and robots can be the perfect team if they don’t step on each other’s toes. Having the latest technology is one thing, but if your human and robotic workers are often not coordinated, robotic initiatives fail to realize their expected value.
Orchestration ensures that tasks are handed off seamlessly between humans and robots by understanding their capacities and planning out which work they will execute at what times. When a robot finishes moving a pallet, a human worker will pick up the next task. Conversely, if a human is prepping an order, robots are ready to take over when it’s time to transport or load. This smooth collaboration reduces delays, maximizes output, and keeps human and robotic workers operating at peak efficiency.
Space and Constraint Optimization: Understanding Bottlenecks In a Facility
Space is a finite resource in any warehouse, and using it wisely is critical. With narrow aisles, towering shelves, and complex product layouts, making everything fit while maintaining easy access is no simple task. Poor space management leads to slowdowns, with workers spending extra time navigating the floor or searching for misplaced items.
Orchestration takes a methodical approach to space optimization, considering the physical layout and the operational constraints that come with it. It factors in product sizes, aisle widths, and even the number of doors available relative to order times to ensure that every square foot is used efficiently. As work is planned, constraints like space, equipment, and product flow are managed to ensure that no one component stops the operation. If potential issues are on the horizon, they are called out well ahead of time, and the orchestration platform will create alerts for management to review. This gives every site a balanced operation that has the potential to maximize throughput, with every action taken now done so in confidence that the site is not compromising the future state of the facility.
Conclusion: Why Orchestration Is Essential
Today’s warehouse operations are more complex and demanding than ever before. It’s no longer enough to “be better.” It would be best if you were different, innovative, and smart in handling every moving part of your operation. Tools like AutoScheduler.AI bring orchestration to the forefront, helping you streamline labor, keep inventory moving efficiently, and optimize space in ways that directly impact your bottom line.
With the four pillars of Labor Planning, Inventory Flow Management, Human/Robotic Task Handoffs, and Space and Constraint Optimization, you can ensure your warehouse doesn’t just survive the demands of today’s environment—it thrives.
About the Author:
Keith Moore is the CEO of AutoScheduler.AI, which orchestrates warehouse activities directly on top of a WMS, optimizing operations for peak performance. Developed alongside industry leaders like P&G and successfully deployed at prominent companies such as Pepsi, General Mills, and Unilever, the AI and Machine Learning platform seamlessly integrates with existing systems. Focused on labor planning, inventory workflow, human-robotics interaction, and space utilization, AutoScheduler.AI streamlines operations, reducing travel and inventory handling while maximizing OTIF rates and labor efficiency. With prescriptive analytics driving insights, clients harness the power to enhance efficiencies and generate value across their supply chains.