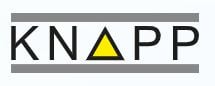
KNAPP launches shuttle for freezer applications
OSR Shuttles Technology released for sale across North American Cold Chain
KNAPP has announced that they will commence the sale and implementation of their industry-leading OSR shuttle technology for cold chain applications and projects.
Regarded as one of the most demanding application categories for any type of automated storage & retrieval application, KNAPP announced that it has completed a rigorous testing process in a beta testing application that includes conveyor hardware, AS/RS shuttles, and software. The successful beta test included over 2 million cycles and 7000 miles of travel. Israel’s leading supermarket chain, Shufersal, is the first customer to implement the solution. This 294,000 square feet fulfillment center covers all temperature zones for its e-commerce food retail business.
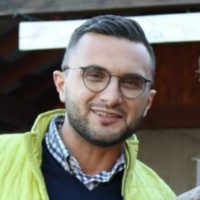
Jusuf Buzimkic
Cold chain technology has been frequently used since the 1950s when it was used to preserve animal-based tissue. As medical breakthroughs have increased, including Covid 19 and other vaccinations, so needs innovative cold chain automation solutions. According to Jusuf Buzimkic, CSO of KNAPP Inc., “The company is uniquely positioned to enter this market and rapidly succeed as it is currently a market leader in ‘track and trace’ technology, software, and shuttle-based automation.”
Another factor that contributes to the prospective success of KNAPP is the desire on the part of cold chain operators to keep workers out of the harsh freezer environment which is both costly and hard to staff.
According to Mr. Buzimkic, some other factors and synergies have driven KNAPP’s interest in this market, including:
- Automation solutions help to address labor volatility.
- Automating work in the freezers by giving tasks to robots is safer
- Cold-chain warehouses are typically tasked with assembling pallets containing different products. KNAPP mixed load palletizing technology includes a unique set of attributes that are conducive to the needs of many cold chain operators.
- Manual warehouses often use reach trucks operated by human workers in freezers, but those pieces of equipment have height limitations, around five or six levels.
- Automated warehouses often use automated storage and retrieval systems (ASRS), which deploy cranes and shuttles programmed to retrieve pallets as directed by warehouse management systems (WMS). That configuration allows freezers to be built taller, which has several advantages.
- Taller freezers create a greater density of products in the same footprint and can reduce the land costs for the cold-chain warehouse.
- Building taller contributes to more efficient building designs. These high-density structures are much more efficient to cool. Additionally, the openings in the freezer get a lot smaller because you have only a conveyor and a pallet or a box moving through a smaller aperture.
- Robots are more accurate and systems calculate up front how they’re going to build out a pallet and how to load it in an economical way.