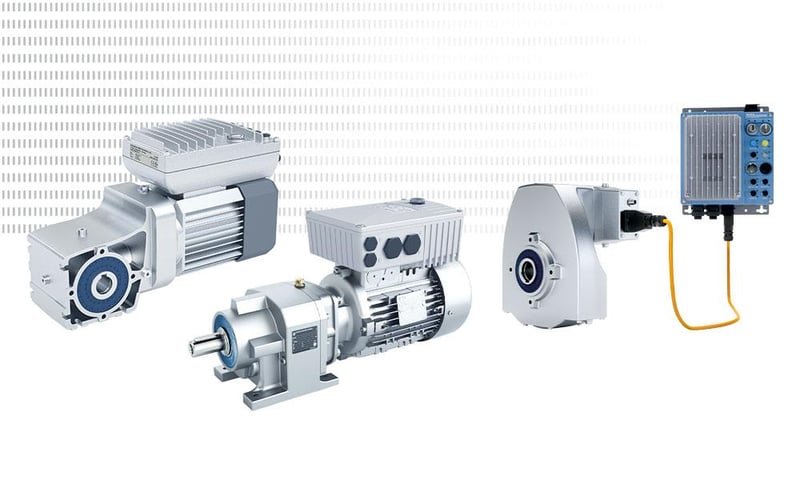
NORD DRIVESYSTEMS will attend MODEX with dynamic solutions for intralogistics
NORD’s drive solutions provide intralogistics systems with reliable operation, dynamic control, and long service life to effectively operate with greater system availability.
NORD’s versatile modular product system offers highly configurable, energy-efficient, and reliable solutions to meet specific supply chain application requirements. The MODEX 2024 exhibition will be open March 11th – 14th at the Georgia World Congress Center in Atlanta, GA. Global drive solutions manufacturer, NORD DRIVESYSTEMS, will be in attendance to showcase their latest innovations for intralogistics applications. NORD has thousands of drives installed across the world and offers complete drive solutions specialized for intralogistics handling such as simple commissioning, Plug-and-Play capabilities, standardization, energy savings, and more.
NORD DRIVESYSTEMS will be exhibiting at Booth C8066 with these industry-focused products:
NORDAC ON/ON+ variable frequency drives were designed with the special requirements of horizontal conveyor technology in mind and have been optimized for use with IE3 motors (NORDAC ON) as well as IE5+ synchronous motors (NORDAC ON+). The electronic drives deliver a compact, dynamic solution for IIoT environments with their full Plug-and-Play capabilities, integrated multi-protocol Ethernet interface, and
when operated with the NORDCON software tool, the drive can be controlled and programmed via PC. The drives offer additional flexibility with motor or wall mounting possible depending on installation space.
NORD’s IE5+ synchronous motors help reduce system variants and operating costs thanks to their high efficiency and constant torque over a wide speed range. The ventilated design effectively dissipates heat to support high overload capacity in intralogistics. The motors are manufactured in-house for quick delivery times and fully match NORD’s modular system of gear units and variable frequency drives. When IE5+ motors are included in a drive system, there is a significant reduction in the Total Cost of Ownership (TCO) and a faster return on investment.
The LogiDrive® solution from NORD is a complete drive solution that reduces planning and commissioning efforts through a cost-effective, standardized design. LogiDrive is ideal for post and parcel, warehouse, and airport systems and for each area, there are advanced versions utilizing IE5+ synchronous motors and a basic version with IE3 asynchronous motors. The advanced versions provide a solution focused on issues such as energy efficiency, version reduction, and TCO while the basic version’s main concentration is reduction of operational costs.
NORDBLOC.1 two-stage helical bevel gear units are designed to optimize system performance, and efficiency, and reduce variants. The single-piece, UNICASE housing ensures an accurate alignment of all bearings, internal shafts, and gears for long service life with easy maintenance. Flexible installation options including various input and output options, solid and hollow shafts, and versatile mounting make the drives highly adaptable to a wide range of applications. For hygienic environments, a closed housing with a smooth surface is available.
NORDBLOC.1 helical inline gear units offer high versatility for intralogistics applications with 16 compact case sizes to choose from and single, double, or triple gear reductions. They deliver quiet operation and reliable performance in a smooth, easy-to-clean design. These units also do not have installation openings, increasing the stability of the product and preventing material accumulation. NORDBLOC.1 helical inline gear units additionally offer a variety of options including keyless shaft designs with shrink disc and GRIPMAXXTM, foot or flange mounting, reinforced bearings, and more.
Condition Monitoring for Predictive Maintenance, drive, and status data are recorded periodically or continuously to proactively maintain machines and optimize the efficiency of the entire plant. This status based maintenance in place of time-based maintenance enables early detection of undesired operating conditions, allowing for planned downtimes for maintenance – saving operating, service, and material costs as well as extending the operating life of components. Data collected from Condition Monitoring can even determine the optimal time to change oil, ensuring systems are always operating at their highest capacity.