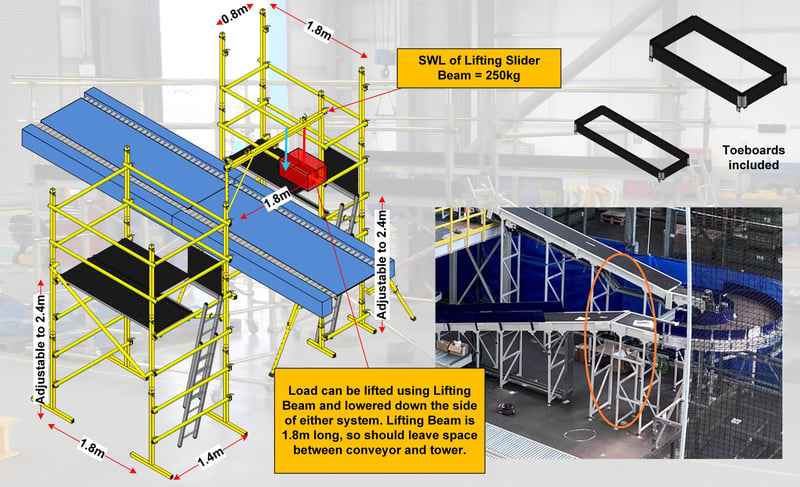
LOBO Systems revolutionizes sortation super hub efficiency with innovative conveyor system application
LOBO Systems, a provider with its evolved scaffolding system, has recently partnered with one of the leading users of automation in the world.
This collaboration aims to address a critical operational challenge in sortation plants; accessing and maintaining motors beneath the conveyor systems.
The global company has a requirement to access and maintain the motors underneath each conveyor system within its hubs and super-hubs. These motors drive the automated system, ensuring the efficient operation of sites. A breakdown in any of these motors could result in significant downtime and require a substantial allocation of resources to resolve the issue, typically involving the hiring of scaffolders.
Admittedly, the usage of a scaffolding company would also resolve the issue faced however, this would result in a major increase in downtime for staff onsite, not to mention the cost implications of hiring in.
The benefit of the LOBO System is that any staff member can be certified, providing they attend a LOBO certification course and pass an examination. This not only minimises downtime but also presents a comprehensive and cost-effective solution to the company. Having members of staff ready to go onsite, once an issue arises, ensures they can be resolved at maximum efficiency.
In the first instance, LOBO delivered an online product demonstration to showcase the system, to highlight its unique safety aspects and discuss potential requirements. After a successful meeting, the LOBO Sales Team created technical drawings to bring the ideas to life (see images).
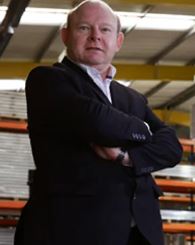
Robert Bokros
“LOBO is thrilled to work closely with such a key-player within the sortation and automation industry” shares Robert Bokros, CEO of LOBO Systems. “This collaboration underscores the team’s capabilities and speaks volumes about our access platform system.” Rob adds.